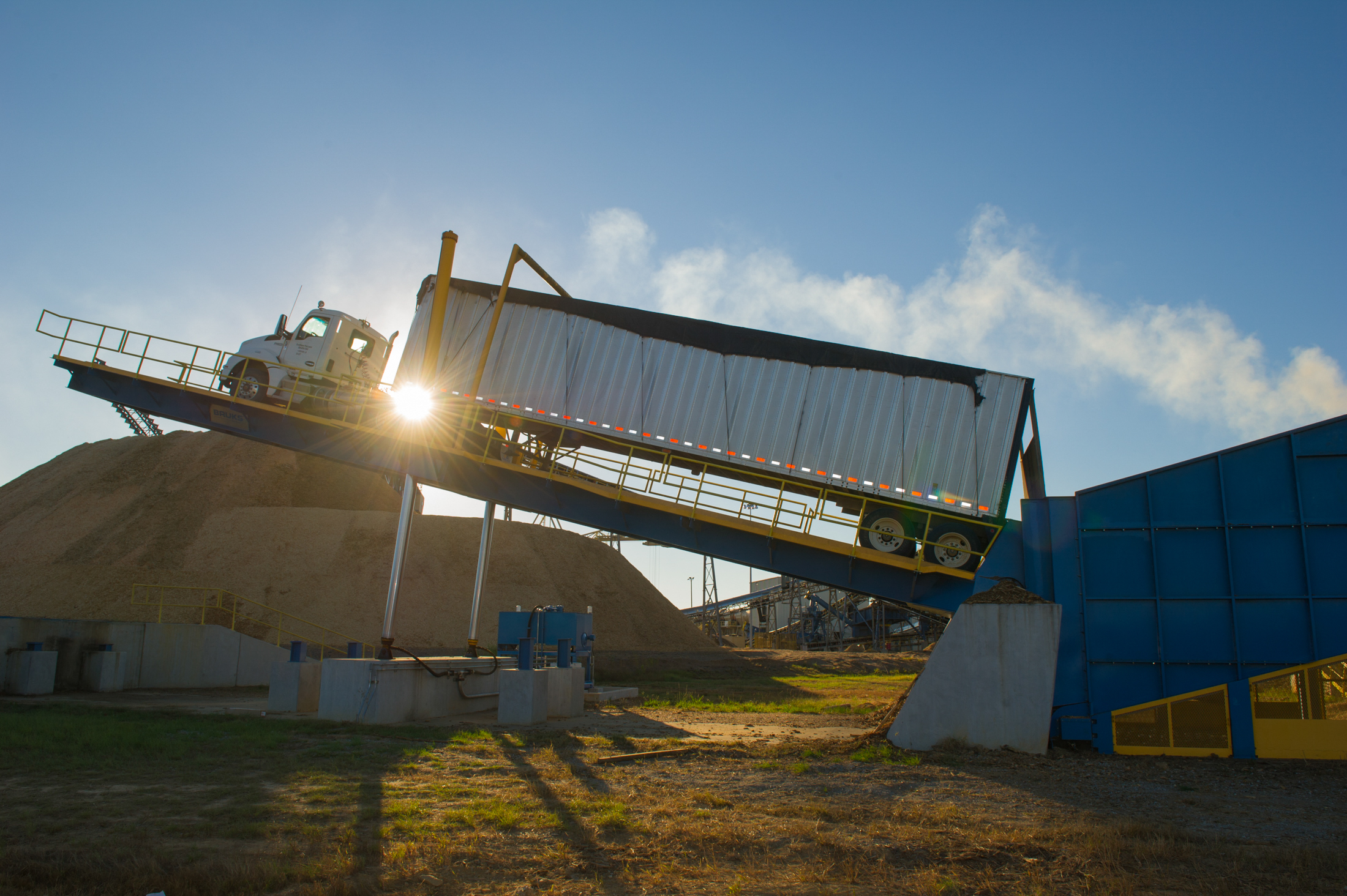
Of all the changes to Drax Power Station over the last decade, perhaps the biggest is one you can’t see. Since converting three of its six generating units from coal to run primarily on compressed wood pellets, Drax has reduced those units’ greenhouse gas (GHG) emissions by over 80%.
And while this is a huge improvement, it would mean nothing if the biomass with which those reductions are achieved isn’t sustainably sourced.
For this reason, Drax works with internationally-recognised certification programmes that ensure suppliers manage their forests according to environmental, social and economic criteria.
Thanks to these certification programmes, Drax can be confident it is not only reducing GHG emissions, but supporting responsible forestry from wherever wood fibre is sourced.
Sustainability certifications
The compressed wood pellets used at Drax Power Station come from various locations around the world, so Drax relies on a number of different forest certification programmes, the three main ones being the Sustainable Forest Initiative (SFI), Forest Stewardship Council® (FSC®)1 and the Programme for the Endorsement of Forest Certification (PEFC).
The programmes share a common goal of demonstrating responsible forest management, but adoption rates vary by region. European landowners and regulators are most familiar with the FSC and national PEFC standards, while North American landowners generally prefer SFI and American Tree Farm System (also members of the PEFC family). In instances in which Drax sources wood pellets carrying these certifications, or in instances in which Drax purchase pellets sourced from certified forests, these certifications offer an additional degree of assurance that the pellets are sustainable.
Over 50% of the pellets used at Drax Power Station come from the southern USA, where SFI and American Tree Farm System are the most widely implemented certification programmes. Overall adoption levels in this region are relatively modest. However, the SFI offers an additional level of certification that can be implemented by wood-procuring entities, such as sawmills, pulp mills and pellet mills.
This programme is referred to as SFI Fiber Sourcing, and to obtain it, participants must demonstrate that the raw material in their supply chains come from legal and responsible sources. These sources may or may not include certified forests. The programme also includes requirements related to biodiversity, water quality, landowner outreach and use of forest management and harvesting professionals. Together, these certification systems have long contributed to the improvement of forest management practices in a region that provides Drax with a significant proportion of its pellets.
And since the SFI and ATFS programmes are endorsed by PEFC, North American suppliers have a pathway for their region’s sustainable forest management practices to be recognised by European stakeholders.
These certification programmes have been in use for many years. But with recent growth in the market for wood pellets, a new certification system has emerged to deal specifically with woody biomass.
New kid on the block
The Sustainable Biomass Program (SBP) was set up in 2013 as a certification system to provide assurance that woody biomass is sourced from legal and sustainable sources. But rather than replacing any previous forest certification programmes, it builds on them.
For example, SBP recognises the evidence of sustainable forest management practices gathered under these other programmes. However, the PEFC, SFI and FSC programmes do not include requirements for reporting GHG emissions, a critical gap for biomass generators as they are obligated to report these emissions to European regulators. SBP fills this gap by creating a framework for suppliers to report their emissions to the generators that purchase their pellets.
When a new entity, such as a wood pellet manufacturer, first seeks certification under SBP, that entity is required to assess its supply base.
Feedstock which has already been certified by another established certification programme (SFI, FSC®, PEFC or PEFC approved schemes) is considered SBP-compliant.
All other feedstock must be evaluated against SBP criteria, and the wood pellet manufacturer must carry out a risk assessment to identify the risk of compliance against each of the 38 SBP indicators.
If during the process a specific risk is identified, for example to the forest ecosystem, the wood pellet manufacturer must put in place mitigation measures to manage the risk, such that it can be considered to be effectively controlled or excluded.
These assessments are audited by independent, third party certification bodies and scrutinised by an independent technical committee.
In conducting the risk assessment, the wood pellet manufacturer must consult with a range of stakeholders and provide a public summary of the assessment for transparency purposes.
Sustainable energy for the UK
Counting major energy companies including DONG Energy, E.ON and Drax as members, the SBP has quickly become an authoritative voice in the industry. At the end of 2016, the SBP had 74 certificate holders across 14 countries – including Drax’s pellet manufacturing arm, Drax Biomass, in Mississippi and Louisiana.
It’s a positive step towards providing the right level of certification for woody biomass, and together with the existing forestry certifications it provides Drax with the assurance that it is powering the UK using biomass from legal and sustainable sources.
Like the fast-reducing carbon dioxide emissions of Britain’s power generation sector, it’s a change you can’t see, but one that is making a big difference.
Read the Drax principles for sustainable sourcing.
1 Drax Power Ltd FSC License Code: FSC® – C119787