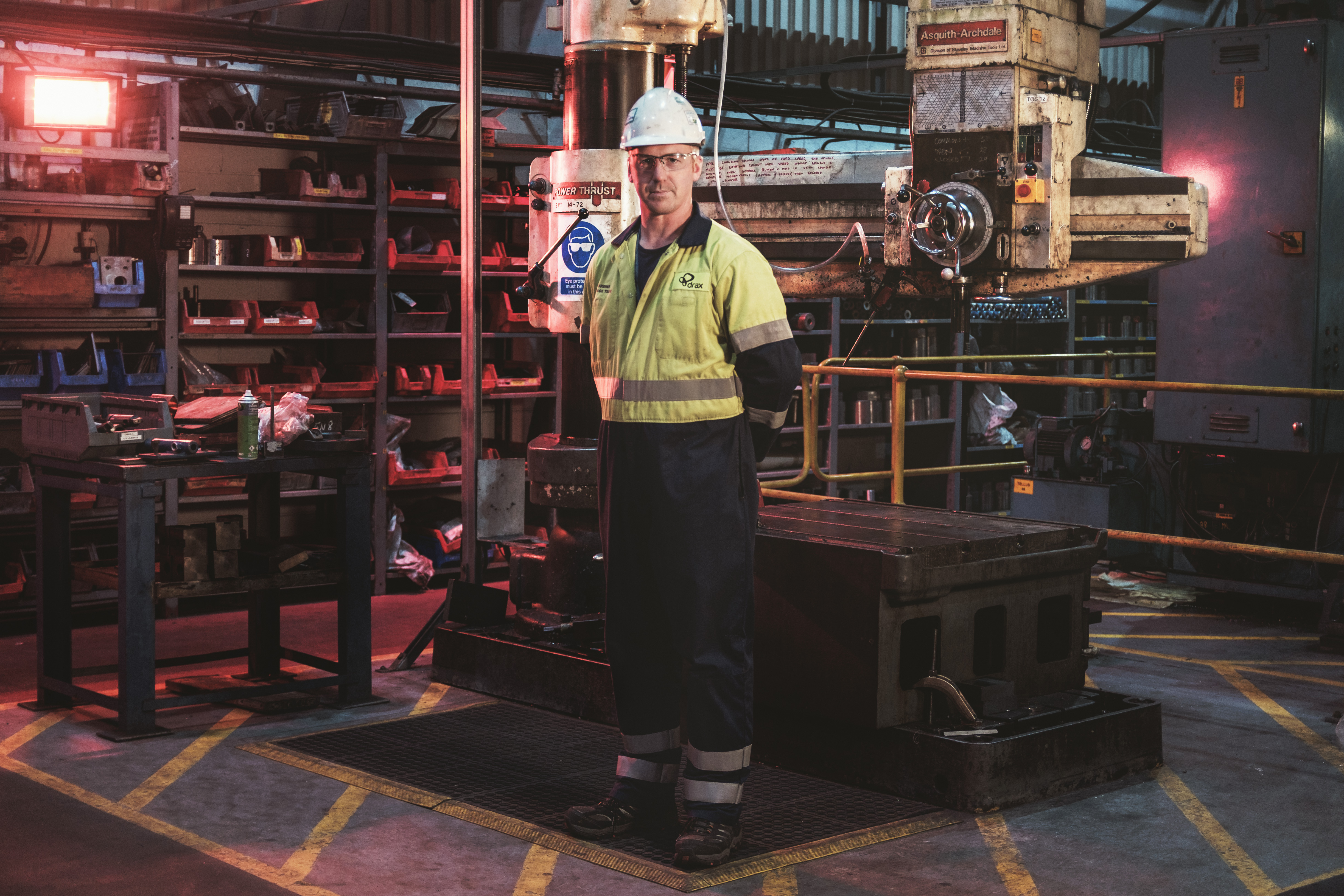
“What can we do to ensure plant integrity, increase plant efficiency and ultimately get more megawatts out of the door for less?” This is a question at the heart of Luke Varley’s work.
Varley is the lead engineer in the turbine section at Drax Power Station, a team who look after arguably the heart of the plant: the steam turbines that drive electricity generation. As well as managing day-to-day maintenance, he and a team of engineers and craftspeople within TSG deliver the major overhaul activities on the turbines to keep them running efficiently and safely.
But as the UK’s largest power station, it’s a site that needs to run all the time – any maintenance needs to fit around that consistent operation. For the most part this happens in the summer months, when electricity demand is lower and parts of the station can be temporarily shut down to carry out repairs. Even though Varley recognises there’s a large cost involved in shutting part of the plant down, it leads to longer term gains.
“We’re taking on work to improve efficiency, because the end result is we’re using less fuel to get more electricity,” he says. A small percentage increase in biomass efficiency can represent huge cost savings, he adds.
But as a relatively new fuel, biomass – in Drax’s case compressed wood pellets – presents a unique challenge for the engineers working with it.
The biomass challenge
In the days when Drax ran only on coal at full load as part of a stable national grid, turbine maintenance meant facing common problems. “Where we had problems which were familiar from one hundred years of turbine history, we knew what to look for,” Varley explains.
But now the plant generates within a far more demanding network that needs flexibility and produces more than half its power using compressed wood pellets, there’s a need for greater efficiency – it means more innovative thinking and new challenges.
For example, most plants in the industry take each turbine offline to maintain it every eight-to-ten years. But using wood pellets means the turbines need to be as efficient as possible, and this means more regular inspections.
“Every four years we go back, overhaul the module and maximise its efficiency again. That’s new to the industry within the UK. Nobody else is doing that,” he says.
Despite the challenges, Varley isn’t fazed. “The technical and management challenges, they both come with experience,” he explains. His engineering experience began before his start at Drax.
“As a sixteen-year-old I walked out into the turbine hall and looked down and thought, ‘this is a different game.’”
Destined for grease
“My dad’s been in engineering all his life. He’d be building a car and I’d be dragged to a scrap man to help take an engine block out of an old car so he could use it at home,” Varley says. “I was destined to always be covered in grease.”
So when it came to beginning his career, Varley was set on what path he wanted to take. Two options presented themselves: working as a trainee draftsman in an air conditioning company or taking an apprenticeship with National Power. An early visit to Drax helped make his decision.
“Even though I’d been around engineering with my dad, as a sixteen-year-old I walked out into the turbine hall and looked down and thought, ‘this is a different game.’” He took the apprenticeship which led him to a number of power plants, but the impression of the Drax turbine hall never left him.
“Later in my career I spent a lot of my time going around different power stations, and in grandness and scale I’ve never come across anything that matches what we’ve got at Drax. So when this job came about and I was asked to join, I said, ‘Sounds good to me.’”
Today, his position of getting more megawatts out of the door for less whilst ensuring safe operation of the plant is one that comes with a lot of responsibility and is built on a long history.
“The guy who was doing this job before me took a lot of pride in it. He used to say, ‘I’ve been here man and boy, I was even here when it was built and I wouldn’t have retired until I knew it was in safe hands.’”
Varley says, “I suppose that’s the best recognition I could get, really.”