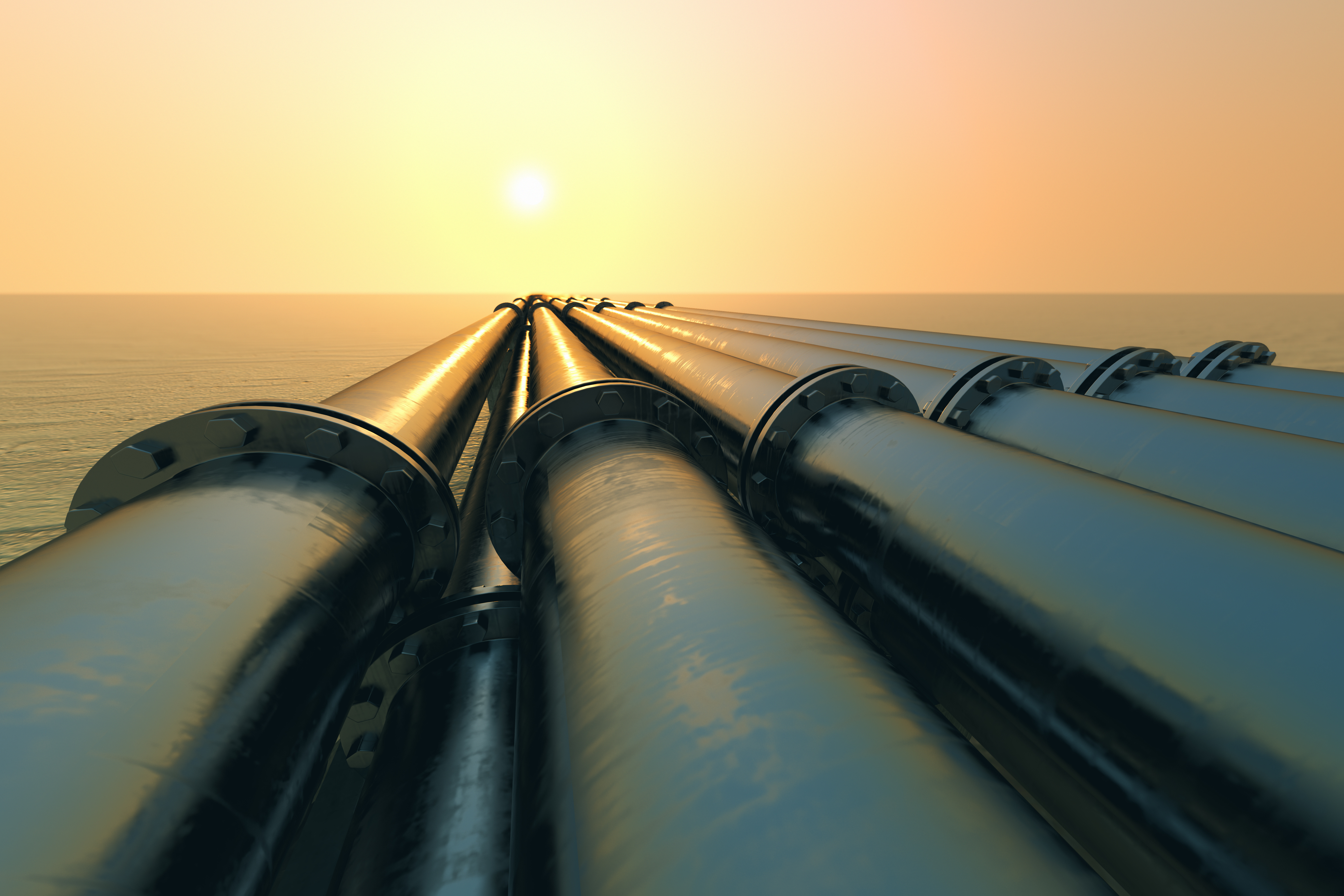
This story was updated in June 2018 following the announcement of Drax’s pilot BECCS project.
Is there a way to generate electricity not only with no emissions, but with negative emissions?
It’s an idea that, after decades of being reliant on coal had seemed almost impossible. But as Drax has shown by announcing a pilot of the first bioenergy carbon capture storage (BECCS) project of its kind in Europe, it might not be impossible for much longer.
A few years on from the historic Paris Agreement – which sets a target of keeping global temperature rise below two degrees Celsius – innovative solutions for reducing emissions are critical. Among these, few are more promising than BECCS.
It sounds like a straightforward solution – capture carbon emissions and lock them up hundreds of metres underground or turn the carbon into useful products – but the result could be game-changing: generating electricity with negative emissions.
Capturing carbon
Carbon capture and storage (CCS) technology works by trapping the carbon dioxide (CO2) emitted after a fuel source has been used and moving it to safe storage – often in depleted oil and gas reservoirs underground.
There are a number of CCS technologies available but one of the simplest is oxyfuel combustion. Fuel such as coal, gas or biomass, is burnt in a high oxygen environment and CO2 – rather than carbon (C) or carbon monoxide (CO) – is produced. Other impurities are removed and the resulting pure CO2 is compressed to form a liquid. This CO2 can then be transported via pipeline to its designated storage space, normally hundreds of metres underground.
The UK is well-placed to benefit from the technology thanks to the North Sea – which has enough space to store the EU’s carbon emissions for the next 100 years.
It’s a technology that can drastically reduce the emissions from fossil fuel use, but how can it be used to produce negative emissions?
Two technologies, working as one
Biomass, such as sustainably sourced compressed wood pellets, is a renewable fuel – the CO2 captured as part of its life in the forest is equal to the emissions it releases when used to generate electricity. When coupled with CCS, the overall process of biomass electricity generation removes more CO2 from the atmosphere than it releases.
A report published by the Energy Technology Institute (ETI) looking at the UK has suggested that by the 2050s BECCS could deliver roughly 55 million tonnes of net negative emissions a year – approximately half the nation’s emissions target.
It’s not the only body heralding it as a necessary step for the future. The Intergovernmental Panel on Climate Change (IPCC), stated in a 2014 report that keeping global warming below two degrees Celsius would be difficult if BECCS had limited deployment.
Support is widespread, but for it to lead to a practical future, BECCS needs suitable support and investment.
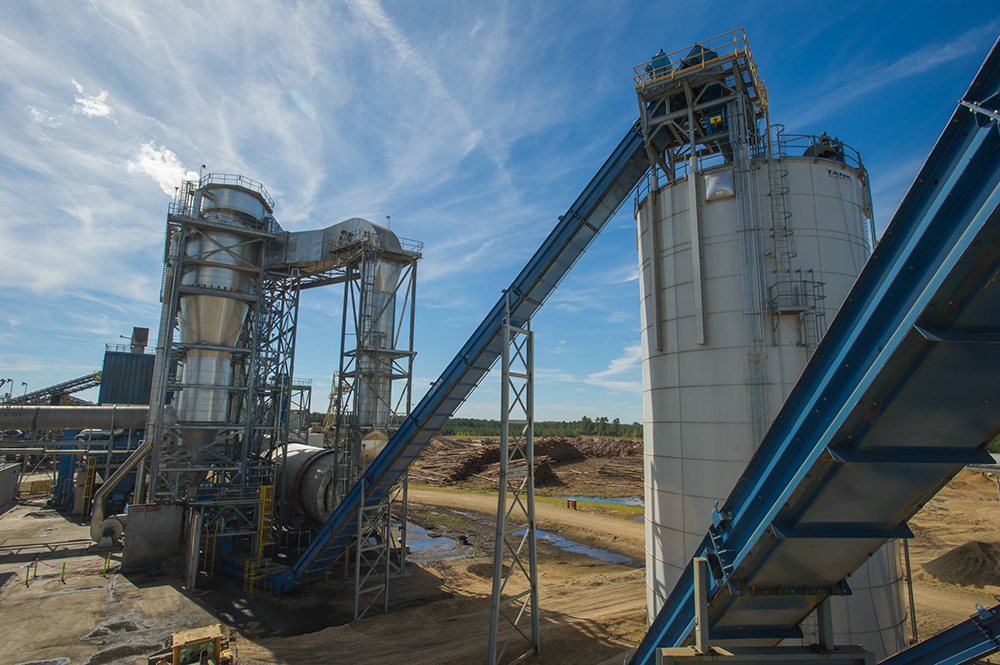
Mills such as Morehouse BioEnergy manufacture compressed wood pellets – a sustainably-sourced fuel for BECCS power plants of the future.
Positive support for negative emissions
There are only a handful of CCS projects in operation or under construction across the world and many simply re-use rather than capture the CO2. Part of the reason is cost. It’s estimated that optimal CCS technology can cost about as much as the power station itself to install, and running it can consume up to 20% of a station’s power output. This means more fuel is needed to produce the same amount of power compared to a conventional power plant of similar efficiency.
Without government support, it remains a prohibitively expensive solution for many power generators. With government support in the form of multi-decade contracts, large CCS or BECCS plants could leverage economies of scale. They could deliver energy companies and their shareholders a return on the investments in the long-term.
Drax research and development
Past plans by Drax could have put the company on a timeline towards becoming the world’s first large scale negative emitter of CO2. It would have achieved it firstly with the construction of a CCS power station at its Selby, North Yorkshire site.
The 428 MW White Rose power station was to be fuelled by a mixture of coal and biomass and once in operation, could have paved the way for similar facilities elsewhere as carbon capture technology improved and costs came down, but unfortunately the project never went ahead.
There are some positive signs that carbon capture technologies are developing around the world. The first ‘clean coal’ power station became operational in the US earlier this month – and a second CCS plant is on the way. A UK-backed carbon capture and use (CCU) project in India recently opened at a chemicals factory, involving the capture of emissions for use in the manufacturing process.
Back in the UK, where the government outlined plans to end coal-fired power generation by 2025, carbon capture power stations must become financially competitive if they are to become a major part of the country’s low carbon future. But if the world is to achieve the targets agreed in Paris and pursue a cleaner future, negative emissions are a must, and BECCS remains a leading technology to help achieve it.