From traffic pollution to household recycling and access to green spaces, cities and governments around the world are facing increasing pressure to find solutions to a growing number of urban problems.
One of these which doesn’t come up often is sewage. But every day, 11 billion litres of wastewater from drains, homes, businesses and farms is collected across the UK and treated to be made safe to re-enter the water system.
Although for the most part sewage treatment occurs beyond the view of the general population, it is something that needs constant work. If not dealt with properly, it can have a significant effect on the surrounding environment.
Of the many ways that sewage is dealt with, perhaps one of the most innovative is to use it for energy. Daldowie fuel plant, near Glasgow is one such place which processes sewage sludge taken from the surrounding area into a renewable, low carbon form of biomass fuel.
The solution in the sludge
In operation since 2002, Daldowie was acquired by Drax at the end of 2018 and today processes 35% of all of Scotland’s wastewater sludge, into dry, low-odour fuel pellets.
“We receive as much as 2.5 million tonnes of sludge from Scottish Water a year,” says Plant Manager Dylan Hughes who leads a team of 71 employees, “And produce up to 50,000 tonnes of pellets, making it one of the largest plants of this kind in the world.”
“We have to provide a 24/7, 365-day service that is built into the infrastructure of Glasgow,” he explains.
This sludge processed at Daldowie is not raw wastewater, which is treated in Scottish Water’s sewage facilities. Instead, the sludge is a semi-solid by-product of the treatment process, made of the organic material and bacteria that ends up in wastewater from homes and industry, from drains, sinks and, yes, toilets.
Until the late 1990s, one of Great Britain’s main methods of disposing of sludge was by dumping it in the ocean. After this practice was banned, cities where left to figure out ways of dealing with the sludge.
Using sludge as a form of fertiliser or burying it in landfills was an already established practice. However, ScottishPower, instead decided to investigate the potential of turning sludge into a dry fuel pellet, that could offer a renewable, low carbon substitute to coal at its power plants.
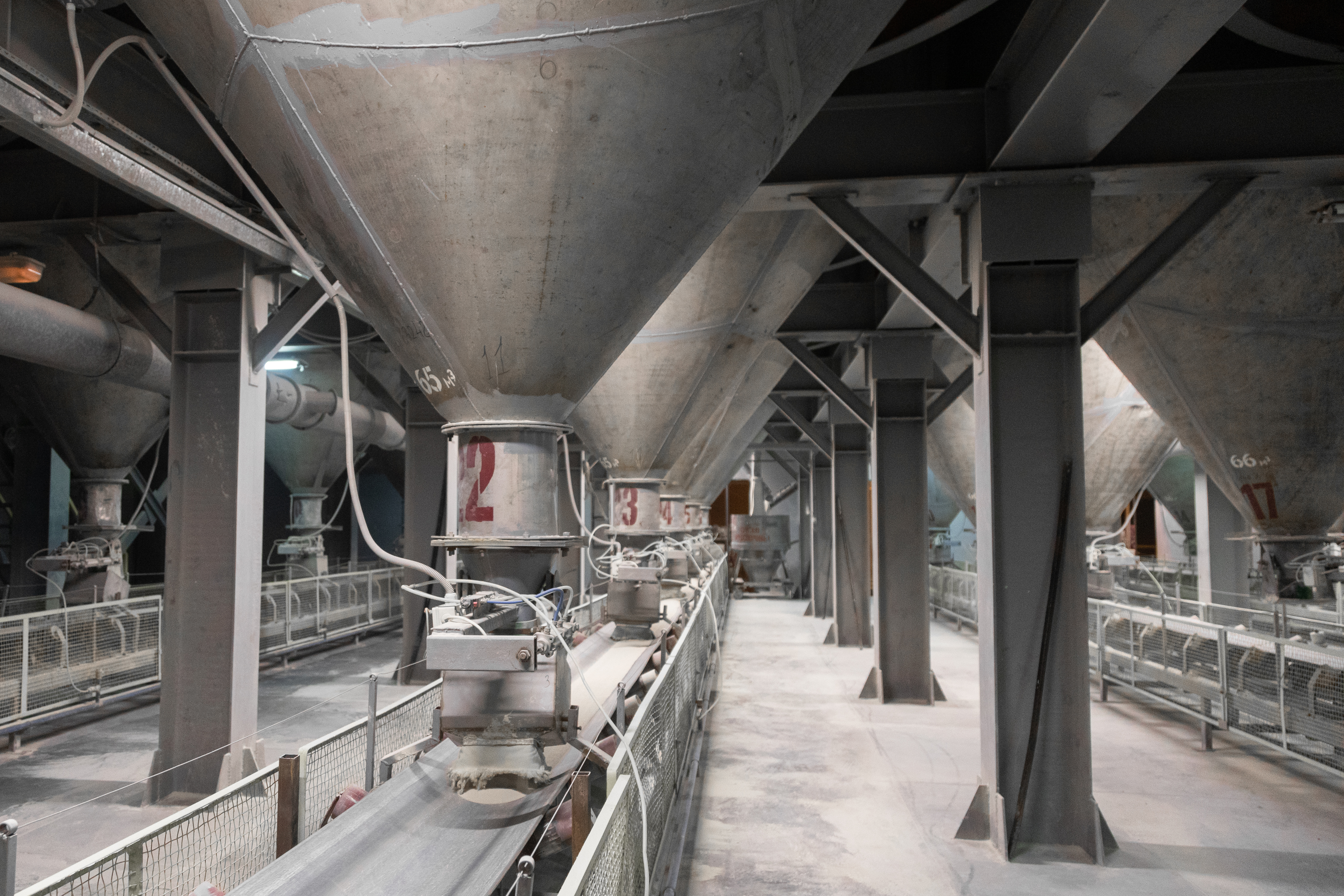
Cement manufacturing fuel kilns
Daldowie was originally designed to supply fuel to Methil Power Station near Fife, which ran on coal slurry. However, it was decommissioned in 2000, before Daldowie could begin delivering fuel to it. This led the plant to instead provide fuel to Longannet Power Station where it was used to reduce its dependency on coal, before it too was decommissioned in 2016.
Today Daldowie’s pellets are used in England and Scotland to fuel kilns in cement manufacturing – an industry attempting to navigate the same decarbonisation challenges as power generation which Daldowie was established to tackle.
Though the end use of the fuel has changed, the process through which the facility transforms the waste remains the same.
The process of turning waste to energy
The process starts after wastewater from Glasgow and the surrounding area is treated by Scottish Water. Daldowie receives 90% of the sludge it processes directly via a pressurised sludge pipeline, the rest is delivered via sealed tanker lorries.
When it arrives at Daldowie, the sludge is 98% water and 2% solid organic waste. It is first screened for debris before entering the plant’s 12 centrifuges, which act as massive spinning driers. These separate water from what is known as ‘sludge cake’, the semi-solid part of the sludge feedstock. This separated water is then cleaned so it can either be used elsewhere in the process or released into the nearby River Clyde.
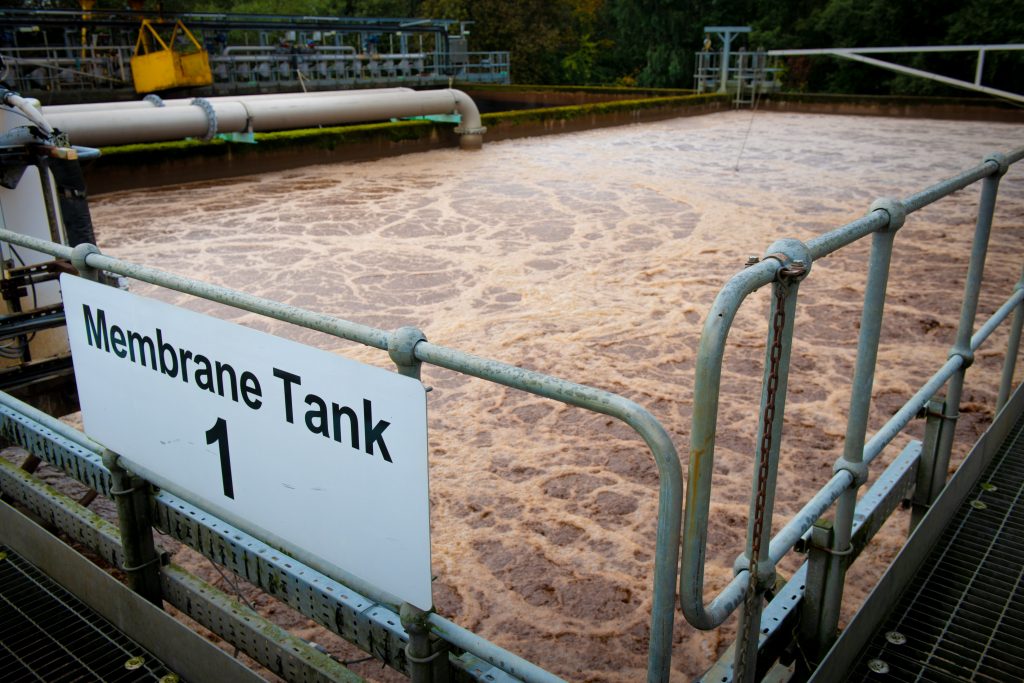
Membrane Tank at Daldowie fuel plant
The remaining sludge cake is dried using air heated to 450 degrees Celsius using natural gas (this also reduces germs through pasteurisation), while the rotating drums give the fuel granules their pellet shape. Once dried the pellets are cooled and inspected for quality. Any material not up to necessary standards is fed back into the system for reprocessing. Fuel that does meet the right standards is cooled further and then stored in silos.
Where possible throughout the process, hot air and water are reused, helping keep costs down and ensuring the process is efficient.
Nearly two decades into its life, very little has had to change in the way the plant operates thanks to these efficiencies. But while the process of turning the waste sludge into energy remains largely unchanged, there is, as always, room for new innovation.
Improving for the future of the site
Daldowie is contracted to recycle wastewater for Scottish Water until 2026. To ensure the plant is still as efficient and effective as possible, the Daldowie team is undertaking a technical investigation of what, if anything, would be needed to extend the life of the plant for at least an additional five years.
“The plant operates under the highest environmental and health and safety standards but further improvements are being planned in 2020.” Hughes explains, “We are upgrading the odour control equipment to ensure we have a best in class level of performance.
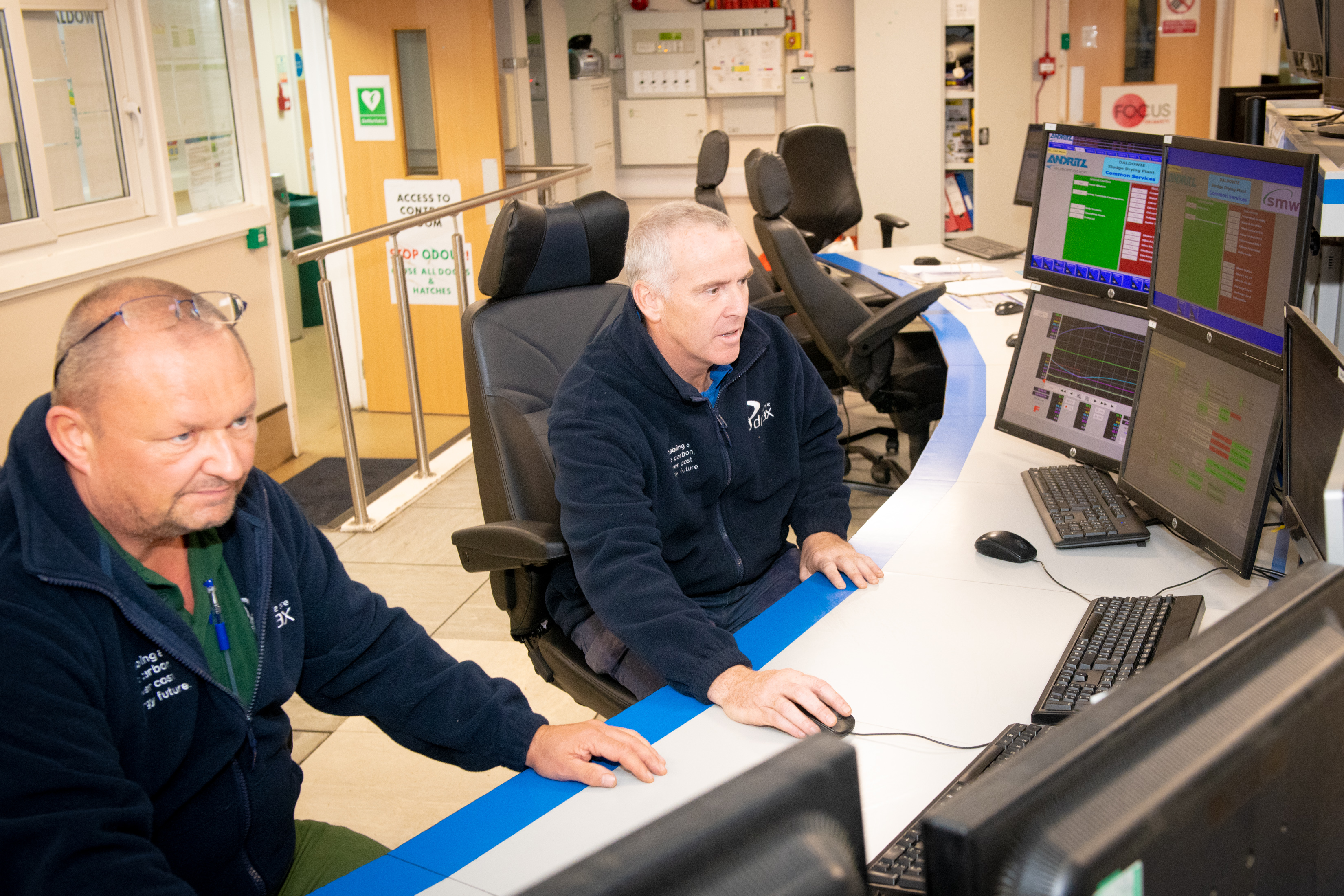
The control room and plant operators at Daldowie
“Drax’s Scotland office, in Glasgow, is working with other industrial facilities in the area, as well as the Scottish Environmental Protection Agency (SEPA), to work with the local community. We are putting in place a series of engagement events, including plant tours from early 2020, offering local residents an opportunity to meet the local team and discuss the planned improvements.”
There are also other potential uses for the fuel, including use at Drax Power Station. As the pellets are categorised as waste and biomass, it would require a new license for the power station.
However, at a time when there is a greater need to reduce the impact of human waste and diversify the country’s energy, it would add another source of renewable fuel to Great Britain’s electricity mix that could help to enable a zero carbon, lower cost energy future.