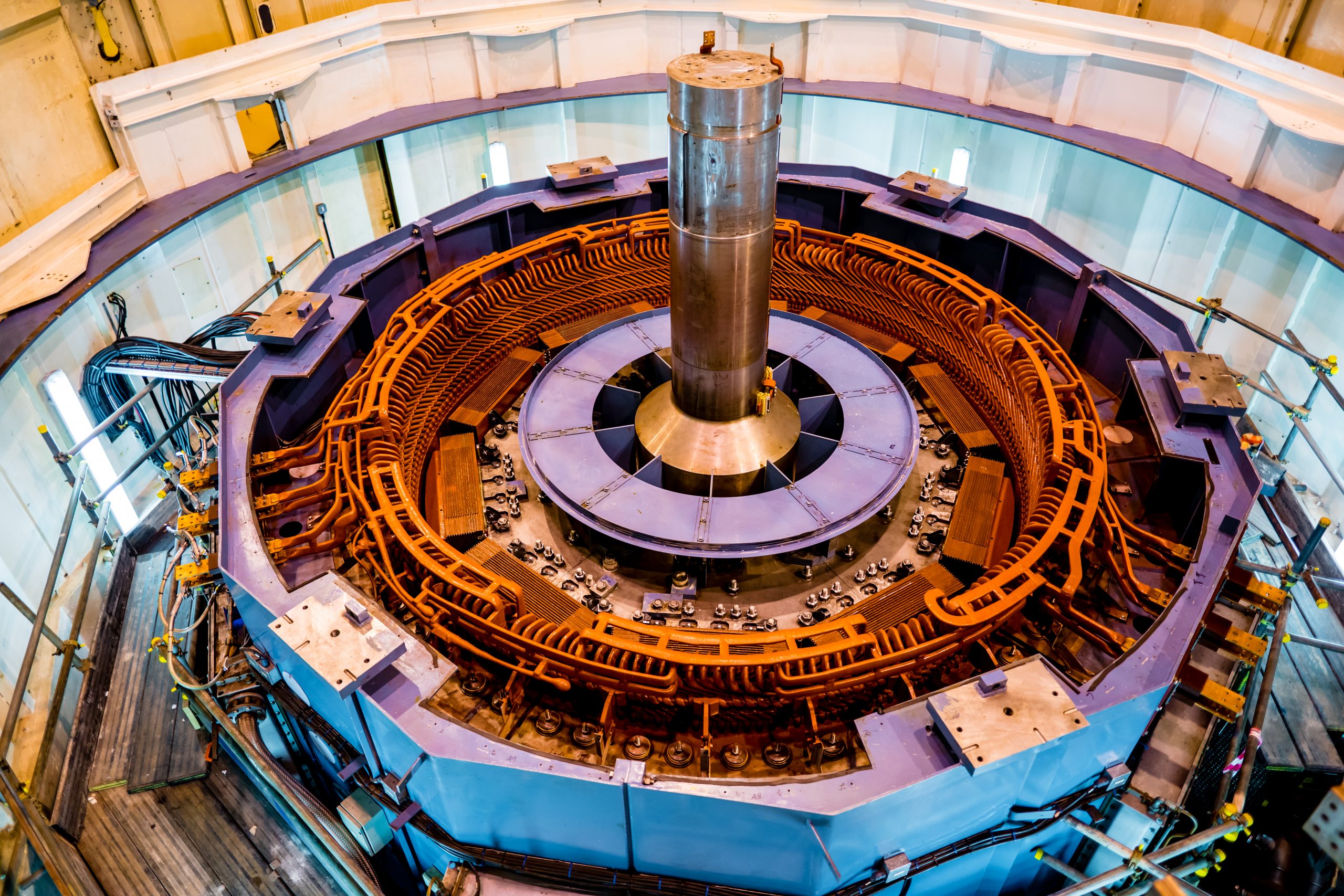
Massive spinning machinery is a big part of electricity generation whether it’s a wind turbine, hydro plant or biomass generator.
But big spinning turbines don’t just pump electricity out onto the grid. They also play a crucial role in keeping the electricity system stable, safe and efficient. This is because big, heavy spinning turbines add something else to the grid: inertia.
This is defined as an object’s resistance to change but in the context of electricity it helps the grid remain at the right frequency and voltage level. In short, they help the grid remain stable.
However, as electricity systems in Great Britain and other parts of the world move away from coal and gas to renewables, such as wind turbines, solar panels and interconnectors, the level of inertia on the system is falling.
“We need the inertia, we don’t need the megawatts,” explains Julian Leslie, Head of Networks at the National Grid Electricity System Operator (ESO). “But in today’s market we have to supply the megawatts and receive the inertia as a consequence.”
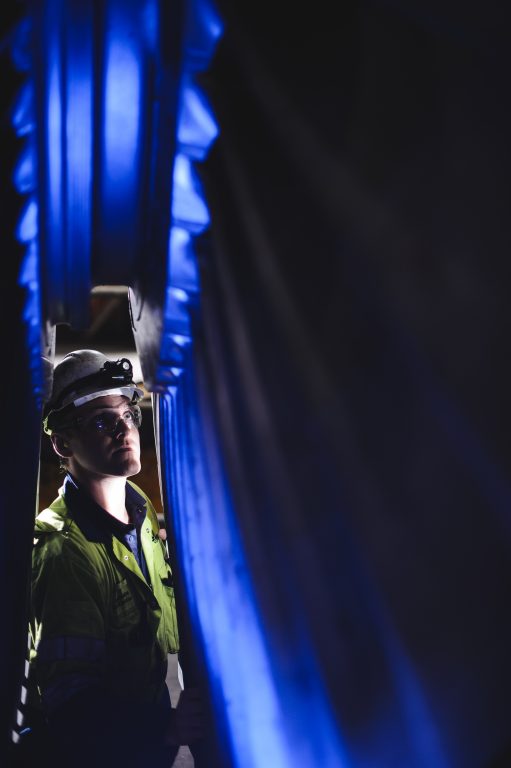
Engineer inspecting turbine blades at Drax Power Station
The National Grid ESO is taking a new approach to this aspect of grid stability by using what are called synchronous condensers. These complicated-sounding pieces of machinery are actually quite straightforward in their concept: they provide inertia to the grid without generating unnecessary power.
These come in the form of:
- Existing generators that remain connected to the grid but refrain from producing electricity.
- Purpose built machines whose only function is to act as synchronous condensers, never generating real power. These may be fitted with flywheels to increase their mass and, in consequence, their inertia.
This means that spinning without generating is about to become a very important part of Great Britain’s electricity system.
Around and around
Electricity generators that spin at 3,000 rpm are described as synchronous generators because they are in sync with the grid’s frequency of 50Hz. These include coal, gas, hydro, biomass turbines and nuclear units. Most spin at 3000 rpm, some machines much less (e.g. 750 rpm). Thanks to the way they are designed, they are all synchronised together at the same, higher speed.
Then there are wind turbines where the generated power is not synchronised to the grid system. Termed asynchronous generators, these machines do not have readily accessible stored energy (inertia) and do not contribute to the stability of the system. Interconnectors and solar panels are also asynchronous.
It’s important that Great Britain’s whole grid is kept within 1% of the 50Hz frequency, otherwise the voltage of electricity starts to fluctuate, damaging equipment, becoming less efficient, even dangerous, or resulting in blackouts.
Say a power station or a wind farm were to drop offline, as occurred in August 2019, this would cause the amount of power on the grid to suddenly fall. But it is not just the power that changes – the frequency and voltage also fluctuate dramatically which can cause equipment damage and ultimately, towns, cities or widespread areas to lose power.
Running machines that have inertia act like the suspension on a car – they dampen those fluctuations, so they are not as drastic. The big spinning machines keep spinning, buying valuable milliseconds for the grid to react, often automatically, before the damage becomes widespread.
However, as a consequence of decarbonisation, more solar panels and wind turbines are now on the system and there are fewer spinning turbines, leading to lower levels of inertia on the grid.
“There are periods when renewable generation and flow from interconnectors are so great that it displaces all conventional, rotational power plants,” says Leslie. “Today, bringing more inertia onto the grid may mean switching off renewables or interconnectors, and then replacing them with rotating plants and the megawatts associated with that.”
Creating a market for inertia and synchronous condensers offers a new way forward – providing inertia without unneeded megawatts or emissions from fossil fuels.
A new spin on grid stability
At the start of 2020, The National Grid ESO began contracting parties, including Drax’s Cruachan pumped-hydro power station, to operate synchronous condensers and provide inertia to the grid when needed.
The plans mark a departure from the previous system where inertia and voltage control from electricity generators was taken for granted.
Cruachan Power Station is already capable of running its units in synchronous condenser mode (one of its units, opened up for maintenance, is pictured at the top of this article). This involves an alternator acting as a motor, offering inertia to the grid without generating unneeded electricity. Other service providers will repurpose existing turbines, construct new machines or develop new technologies that can electronically respond to the grid’s need for stability.
Synchronous condensers, or the idea of spinning a turbine freely without generating power, are not new concepts; power stations in the second half of the 20th century could shut down certain generating units but keep them spinning online for voltage control.
In the 1960s and 70s, some substations – where the voltage of electricity is stepped up and down from the transmission system – also deployed stand-alone synchronous condensers. These were also used to provided inertia as well as voltage control but are long since decommissioned.
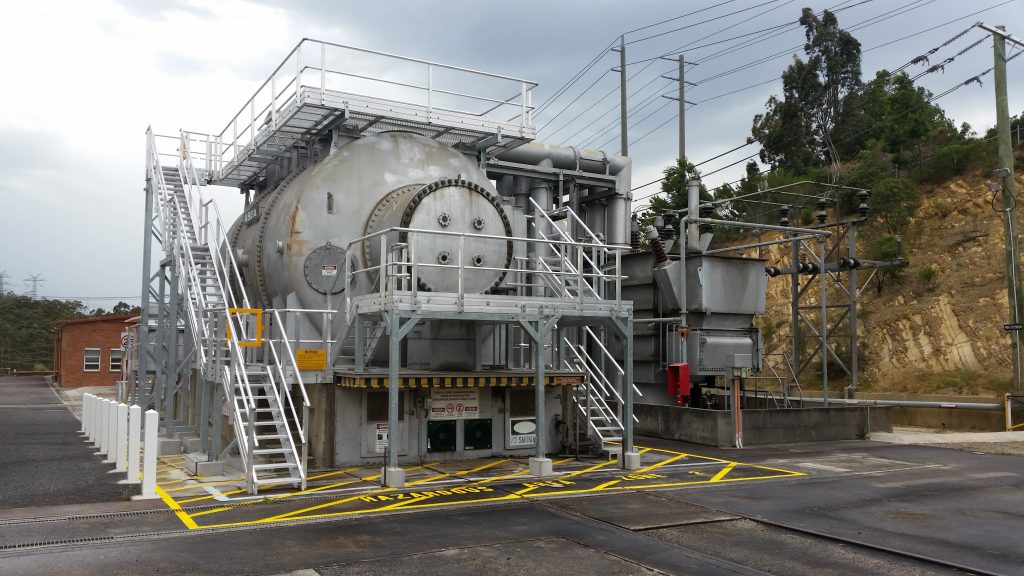
Synchronous condenser installation at Templestowe substation, Melbourne Victoria, Australia. By Mriya via Wikimedia.
“Synchronous condensers are a proven technology that have been used in the past,” says Leslie. “And there are many new technologies we are now exploring that can deliver a similar service.”
Cheaper, cleaner, more stable
The National Grid ESO estimates the technology will save electricity consumers up to £128 million over the next six years. Savings, which come from negating the need for the grid to call upon fossil fuels for inertia as coal, oil and gas, become increasingly uneconomical across the globe as carbon taxes grow.
The fact that synchronous condensers do not produce electricity also saves money the grid may have had to pay out to renewable generators to stop them producing electricity or to storage systems to absorb excess power.
“It means the market can deliver the renewable flow without the grid having to pay to restrain it or to pay for gas to stabilise the system,” says Leslie. “Not only does this allow more renewable generation, but it also reduces the cost to the consumer.”
In a future energy system, where there is an abundance of renewable electricity generations, synchronous condensers will be crucial in keeping the grid stable. The National Grid ESO’s investment in the technology further highlights the importance of new ideas and innovation to balance the grid through this energy transition.
Synchronous generation provides benefits to system stability beyond the provision of inertia. In a subsequent article we’ll also explore how synchronous condensers can assist with voltage stability and help regional electricity networks and customers to remain connected to the national system during and after faults.
Read about the past, present and future of the country’s electricity system in Could Great Britain go off grid?