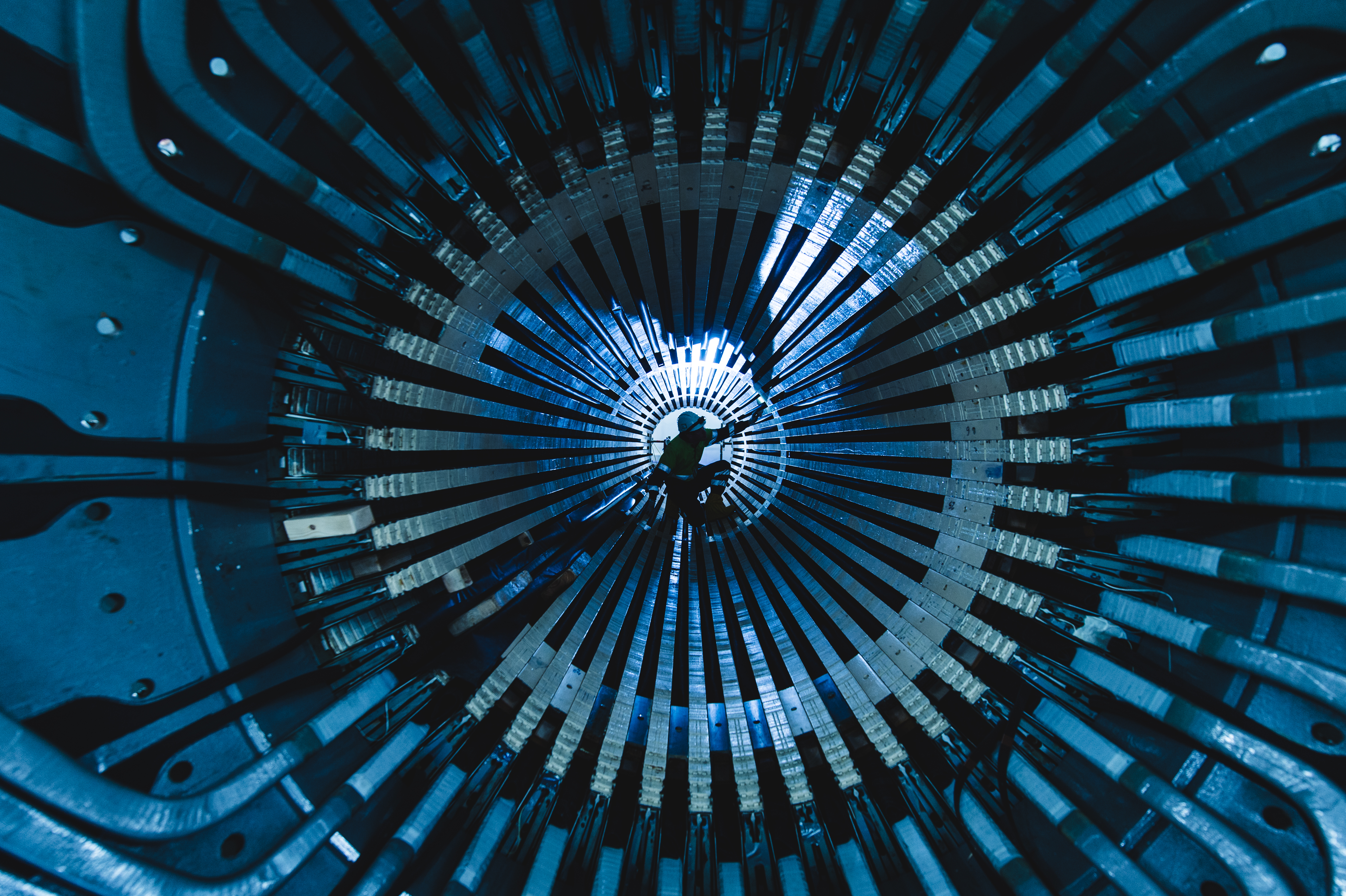
Locked in a Parisian vault and stored in a double set of bell jars is a small cylinder of metal. Made of platinum-iridium, the carefully guarded lump weighs exactly one kilogram. But more than just weighing one kilogram, it is the kilogram from which all other official kilograms are weighed.
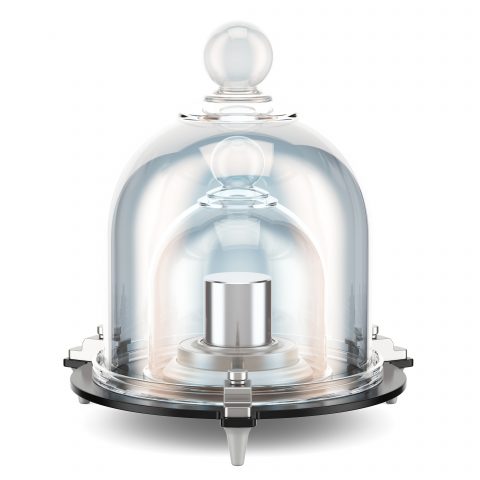
International prototype kilogram with protective double glass bell
Known as the International Prototype Kilogram, or colloquially as Le Grand K, the weight was created in 1889 and has been carefully replicated to offer nations around the world a standardised kilogram. But over time Le Grand K and its clones have slightly deteriorated through wear and tear, despite extremely careful use. In an age of micro and nanotechnology, bits of metal aren’t quite accurate enough to dictate global weighs and so as of May this year it will no longer be the global measurement for a kilogram. An electromagnet is part of its replacement.
An electromagnet is effectively a magnet that is ‘turned on’ by running an electric current through it. Cutting the current turns it off, while increasing or decreasing the strength of the current increases and decreases the power of the magnet.
It can be used to measure a kilogram very precisely thanks to something called a Kibble Balance, which is essentially a set of scales. However, instead of using weights it uses an electromagnet to pull down one side. Because the electric current flowing through the electromagnet can be increased, decreased and measured very, very accurately, it means scientists can define any weight – in this case a kilogram – by the amount of electrical current needed to balance the scale.
This radical overhaul of how weights are defined means scientists won’t have to fly off to Paris every time they need precise kilograms. Beyond just replacing worn-out weights, however, it highlights the versatility and potential of electromagnets, from their use in electricity generation to creating hard drives and powering speakers.
The simple way to make a magnet
Magnets and electricity might at first not seem closely connected. One powers your fridge, the other attaches holiday souvenirs to it. The former certainly feels more useful. However, the relationship between magnetic and electric fields is as close as two sides of the same coin. They are both aspects of the same force: electromagnetism.
Electromagnetism is very complicated and there’re still aspects of it that are unknown today. It was thinking about electromagnetism that led Einstein to come up with his theory of special relativity. However, actually creating an electromagnet is relatively straightforward.
All matter is made up of atoms. Every neutral atom’s core is made up of static neutrons and protons, with electrons spinning around them. These electrons have a charge and a mass, giving the electrons a tiny magnetic field. In most matter all atoms are aligned in random ways and effectively all cancel each other out to render the matter non-magnetic. But if the atoms and their electrons can all be aligned in the same direction then the object becomes magnetic.
A magnet can stick to an object like a paperclip because its permanent magnetic field realigns the atoms in the paperclip to make it temporarily magnetic too – allowing the magnetic forces to line up and the materials to attract. However, once the paper clip is taken away from the magnet its atoms fall out of sync and point in random directions, cancelling out each other’s magnetic fields once again.
Whether a material can become magnetic or not relies on a similar principal as to whether it can conduct electricity. Materials like wood and glass are poor conductors because their atoms have a strong hold over their electrons. By contrast, materials like metals have a loose hold on their electrons and so are good conductors and easily magnetised. Nickle, cobalt and iron are described as ferromagnetic, because their atoms can stay in sync making them a permanent magnet. But when magnets really become useful is when electricity gets involved.
Putting magnets to work
Running an electric current through a material with a weak hold on its electrons causes them to align, creating an electromagnetic field. Because of the relationships between electric and magnetic fields, the strength of the electromagnet can also be altered by increasing or decreasing the current, while switching the flow of the current will flip its north and south poles.
Having this much control over a magnetic field makes it very useful in everyday life, including how we generate electricity.
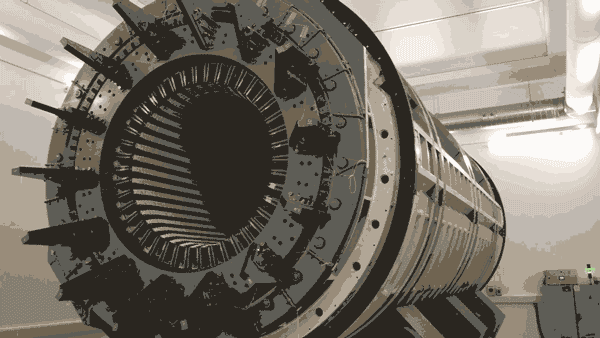
Find out how we rewind a generator core in a clean room at the heart of Drax Power Station
Inside each of the six generator cores at Drax Power Station, is a 120-tonne rotor. When a voltage is applied, this piece of equipment becomes a massive electromagnet. When steam powers the turbines to rotate it at 3,000 rpm the rotor’s very powerful magnetic field knocks electrons in the copper bars of the surrounding stator out of place, sending them zooming through the metal, in turn generating an electrical current that is sent out to the grid. The 660 megawatts (MW) of active power Drax’s Unit 1 can export into the national transmission system is enough to power 1.3 million homes for an hour.
Beyond just producing electricity, however, electromagnets are also used to make it useful to everyday life. Almost anything electric that depends on moving parts, from pumping loud speakers to circuit breakers to the motors of electric cars, depend on electromagnets. As more decarbonisation efforts lead to greater electrification of areas like transport, electromagnets will remain vital to daily life into the future.