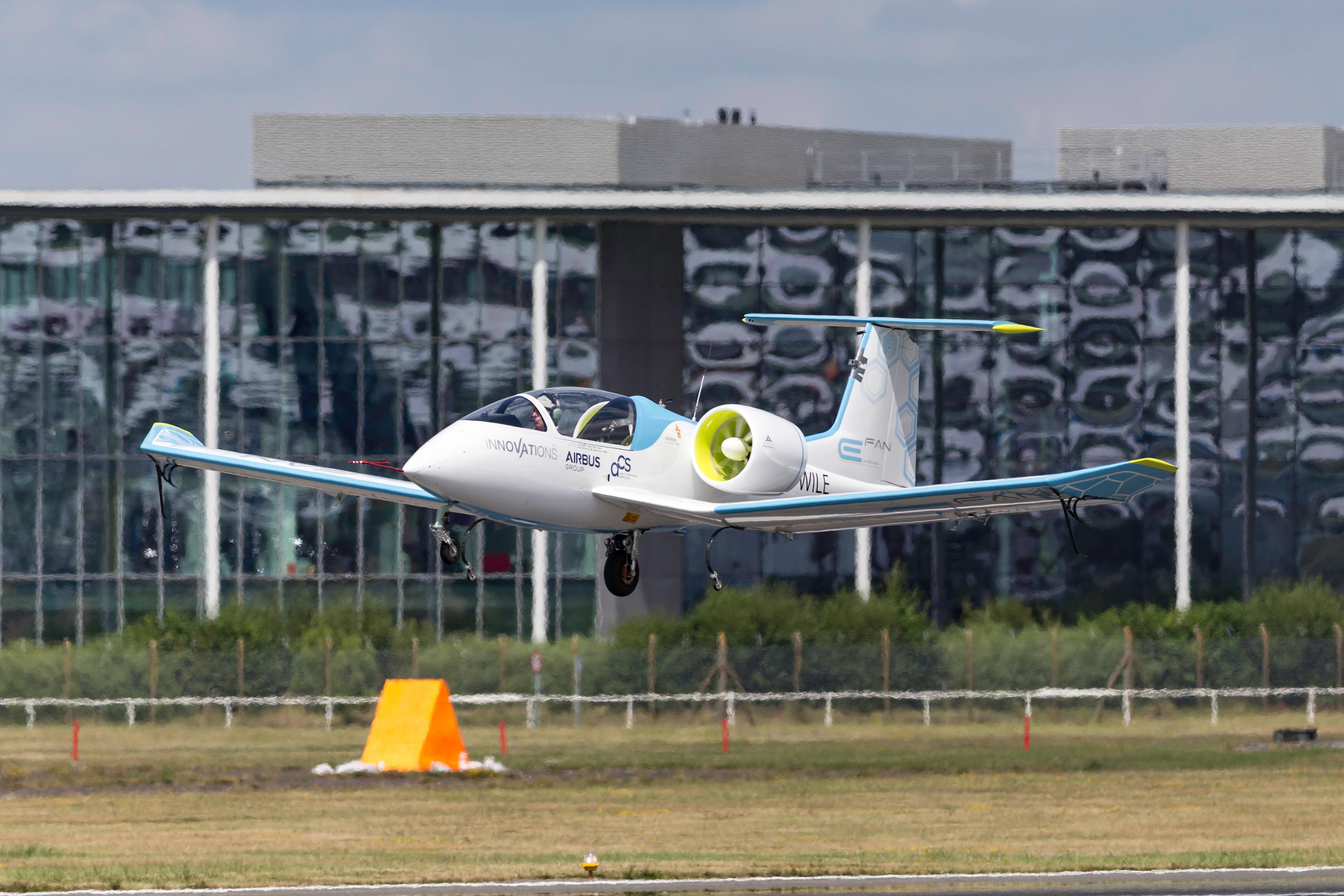
With rapid technological improvements and falls in battery prices, improving performance and reducing the cost, experts predict that by 2050, 90% of new-build cars will be powered by electricity.
However, it’s not only roads where transport is decarbonising; electricity may soon power more of the world’s trains, plus its planes and boats.
Taking trains forward
The electrification of the rail industry has arguably been in the making for a lot longer than EVs but there’s still progress to be made. Trains are already one of the most-efficient modes of long-distance transport, and Network Rail claims electric models’ carbon emissions are 20% to 35% lower than diesel trains. Electric trains also accelerate and brake faster than diesel-powered models, and cause less wear to tracks.
Electrified trains are already commonplace in many parts of the world – Japan’s famously fast and reliable Shinkansen railways are electric. Meanwhile in the UK, less than 50% of the rail network is electrified, with Transport Secretary Chris Grayling’s recent ‘pause’ on development casting doubts on previous ambitious plans to electrify 850-miles of track.
Nevertheless, advancements are still being made to enable the sector to utilise solar energy as an alternative to the national power grid. The concept would prove cost effective and reduce the carbon footprint of trains even further.
According to a report by climate change charity 10:10 and researchers at Imperial College’s Energy Futures Lab, rail companies could cut their annual running costs by millions of pounds through installing their own trackside solar panels to power electric trains directly. With companies spending around £500 million a year on power, the savings on self-generation would enable them to cut fares for passengers, as well as emissions.
Take off for electric planes
Of all transport modes, air travel has made the least progress in electrification but there’s hope yet. Airbus, Rolls-Royce and Siemens recently teamed up to develop the technology needed to create electrically-powered aircraft. The companies plan to fly a demonstrator aircraft with one of its existing jet engines replaced by an electric unit in 2020.
Paul Stein, chief technology officer at Rolls-Royce, said: “Aviation is the last frontier of the electrification of transport. It could lead to a step change in the way we fly with greater efficiency and less noise.”
These proposed hybrid-electric aircraft are not powered by on-board batteries like EVs but with a gas turbine that generates electricity to drive the propellers. This could reduce fuel consumption by up to 10%, predicted Mark Cousin, head of flight demonstration at Airbus.
Moving to electric aircraft would also help the aviation industry meet EU targets of a 60% reduction in emissions of carbon dioxide (CO2) by 2020, as well as 90% less nitrogen oxides and a noise reduction of around 75%.
UK-based airline EasyJet also announced it could be flying electric planes within a decade and is teaming up with US firm Wright Electric to build battery-powered aircraft.
According to EasyJet, the move would enable battery-powered aeroplanes to travel short-haul routes such as London to Paris and Amsterdam, and Edinburgh to Bristol. Wright Electric is aiming for an aircraft range of 335 miles, which would cover the journeys of about a fifth of EasyJet passengers. The challenge comes in making lithium-ion batteries light and safe enough for the air.
The airline said this was the next step in making air travel less harmful for the environment, after cutting carbon emissions per passenger kilometre by 31% between 2000 and 2016. Wright Electric claims that electric planes will save up to 15% in fuel burn and CO2 emissions, be 50% quieter and 10% cheaper for airlines to buy and operate, with the cost saving potentially passed on to passengers.
Testing new waters
There’s a lot of buzz coming out of the maritime industry too. Every year marine transport emits 1,000 million tonnes of CO2, which is why the International Maritime Organization (IMO) has agreed that a reduction of 50% should come by 2050 compared with 2008 levels. Although the deal fell short of more ambitious targets preferred by those ranging from the European Union to environmental NGOs, the IMO did also commit to pursue efforts toward phasing out CO2 emissions entirely.
As Paris Agreement goals to cut carbon dioxide emissions loom, businesses around the world are innovating.
Small fleets of battery-powered boats designed for fjords and inland waterways in Norway, Belgium and the Netherlands are preparing to set sail, including some able to run autonomously without a crew.
Dutch company Port-Liner is also gearing up to launch the first fully-electric, emission-free barges in Europe. Dubbed ‘Tesla’ ships, Port-Liner Chief Executive Officer Ton van Meegen claims these barges would be the first in the world to sail on carbon-neutral batteries. The first six barges alone are expected to remove 23,000 trucks from the roads annually in the Netherlands, replacing them with zero-emission methods of transport.
China also recently launched an electric cargo ship to haul coal which, whilst not doing much for its ambitions to cut pollution, will at least eliminate shipping emissions from diesel engines. Electric ships may not yet be the norm globally but progress is underway to cut the 2.5% of global greenhouse emissions that result from the maritime transport industry.
Once a far-flung fantasy in some areas, electrified transport is fast becoming a reality. EVs and rail are leading the way, but it’s clear the electric transport revolution has a long way to travel.