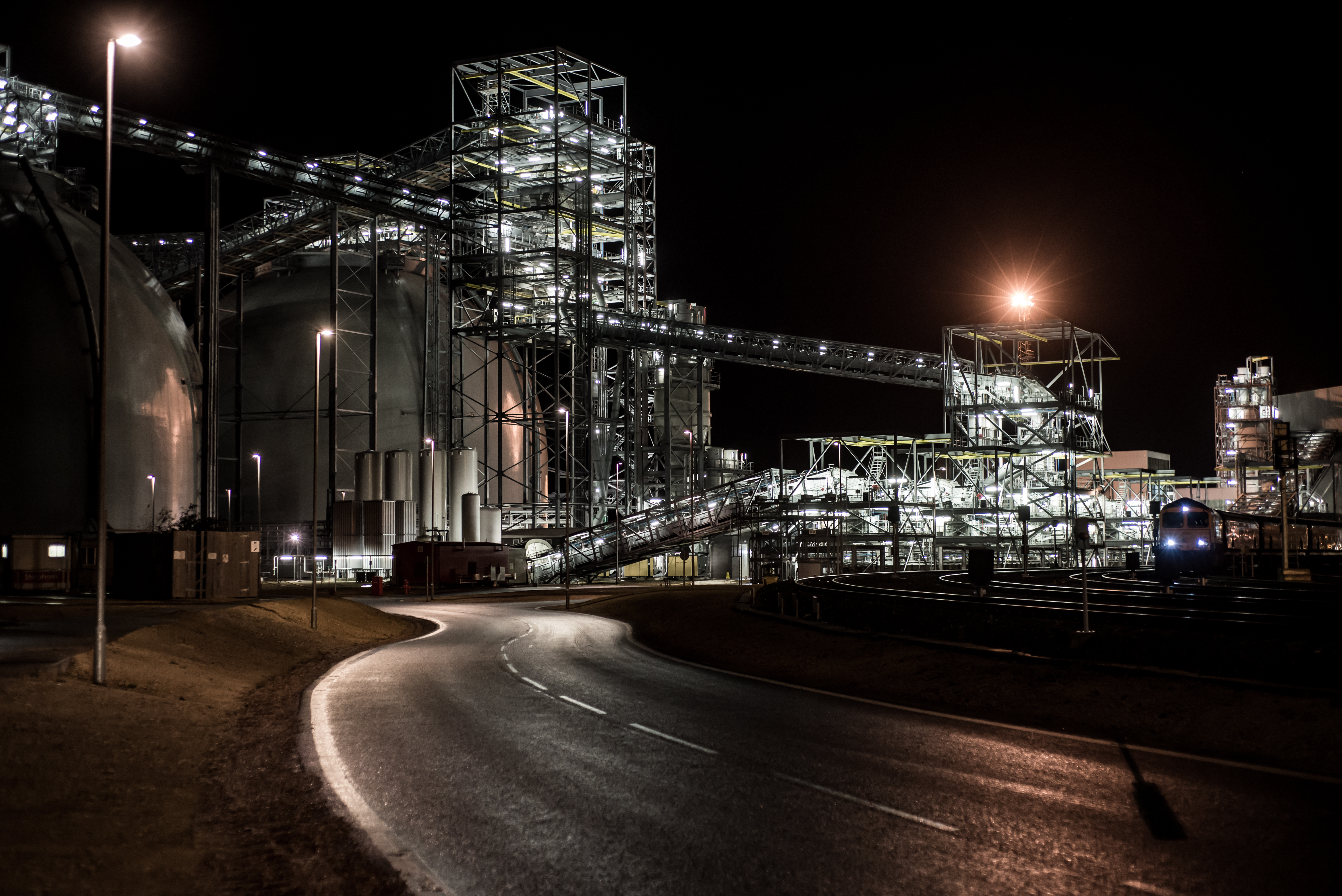
Things are different at night. As darkness falls the familiar sights and sounds that make up daily life retreat, creating a strange yet familiar world. There’s less activity, but that doesn’t mean there is no activity.
While Great Britain sleeps, phones charge and fridges hum. Electricity is a 24-hour need, and so the stations generating it must be 24-hour operations. But the life of a power station by night is very different to that by day.
“Walking around the power station at night can almost feel like the Mary Celeste,” says Simon Acaster, Drax Power Station’s Generation Manager. “There may be as few as 50 to 60 people on site, which isn’t a lot when you consider the size of the plant and compare it to the day, when there are some 650 people around.”
Drax Power Station by day is a hive of activity. Alongside generation there are maintenance, engineering, trading and contract support. At night, this is all stripped back.
“Work is focused on the core production issues: looking after the asset and maintaining power generation output to meet our contract position, keeping the teams safe and making sure we stay environmentally compliant,” says Mark Rhodes, Shift Manager at Drax.
“It’s a quieter place,” he adds.
Keeping power flowing
Typically, teams at Drax swap over at 8pm and 8am on a cycle of day and night shifts. During the summer months, when one or more of the station’s six, 600+ megawatt (MW) units can be on outage and maintenance is carried out across the station, work often continues around the clock right through the night.
But during a period of normal operation, the night workforce is reduced to basic operations and maintenance teams, material handling teams receiving biomass deliveries – which continue through the night – and security staff.
Demand for electricity typically falls overnight, so Drax shuts down unneeded generation units around 10pm. As morning approaches teams prep them to restart in time for when people wake up and turn on kettles.
“Even when we shut the units down, the turbine is still turning throughout the night,” says Acaster. “All the hydraulic pumps and lube oil systems are still functioning. A lot of plant is in service even when the units are shut down.”
This means there’s still the potential, as during the day, for something to need maintenance or attention at any moment requiring the teams to jump into action.
“We aim to sort any short-term issues through the night,” says Rhodes. “But for any technical issues that can wait, we tackle them when the day team returns and we’re fully staffed. At night it’s more about safely managing the asset.”
The hardest part of a running the power station overnight, however, is not a technical one, it’s a human one.
“There’s no doubt about it, working nights is tiring,” says Acaster. “The biggest challenge is keeping everybody focused and aware of what’s happening.”
He continues: “Unit controllers regularly talk to their plant operators, checking in every hour so we know they’re safe. Supervisors need to be out on plant engaging and talking to employees, checking on what they’re doing and keeping them active and alert.”
The shifting of the night shift
The decarbonisation of Great Britain’s electricity system has changed the way Drax operates during the day, and the same is true of the night.
“Historically, we had six units and they would be baseload, generating 645 MW each,” says Rhodes. “They would operate continuously day and night.” But with the demand profile changing, lower power prices, and other methods of generation coming onto the system, that model is changing.
“Overnight is normally the time of least demand and when the price of power becomes most depressed,” Rhodes continues. “So we take units off and prepare them for the morning, returning when there is value.”
Regularly shutting down and starting the units takes a tougher toll on the equipment than running them continuously, which increases the need for maintenance teams on night shifts. There’s also a need for teams to be on standby to ramp up or down generation.
The increased volatility of the country’s power network, brought on in part by increasing levels of intermittent renewables, means National Grid can often ask Drax to increase or decrease generation at short notice to provide balancing services like inertia, frequency response or reserve power.
“Our units can come down to 300 MW and stay at that level,” says Acaster. “Across three units that gives National Grid 900 MW of spare capacity that can be turned up. It’s like a sleeping giant awaiting start up at any time.”
But unlike other sleeping giants this one is never truly at rest. The demands of the network keep it, and the men and women operating it, humming through the night, 24-hours a day. The power station at night is a quieter place, but it is never a silent one.