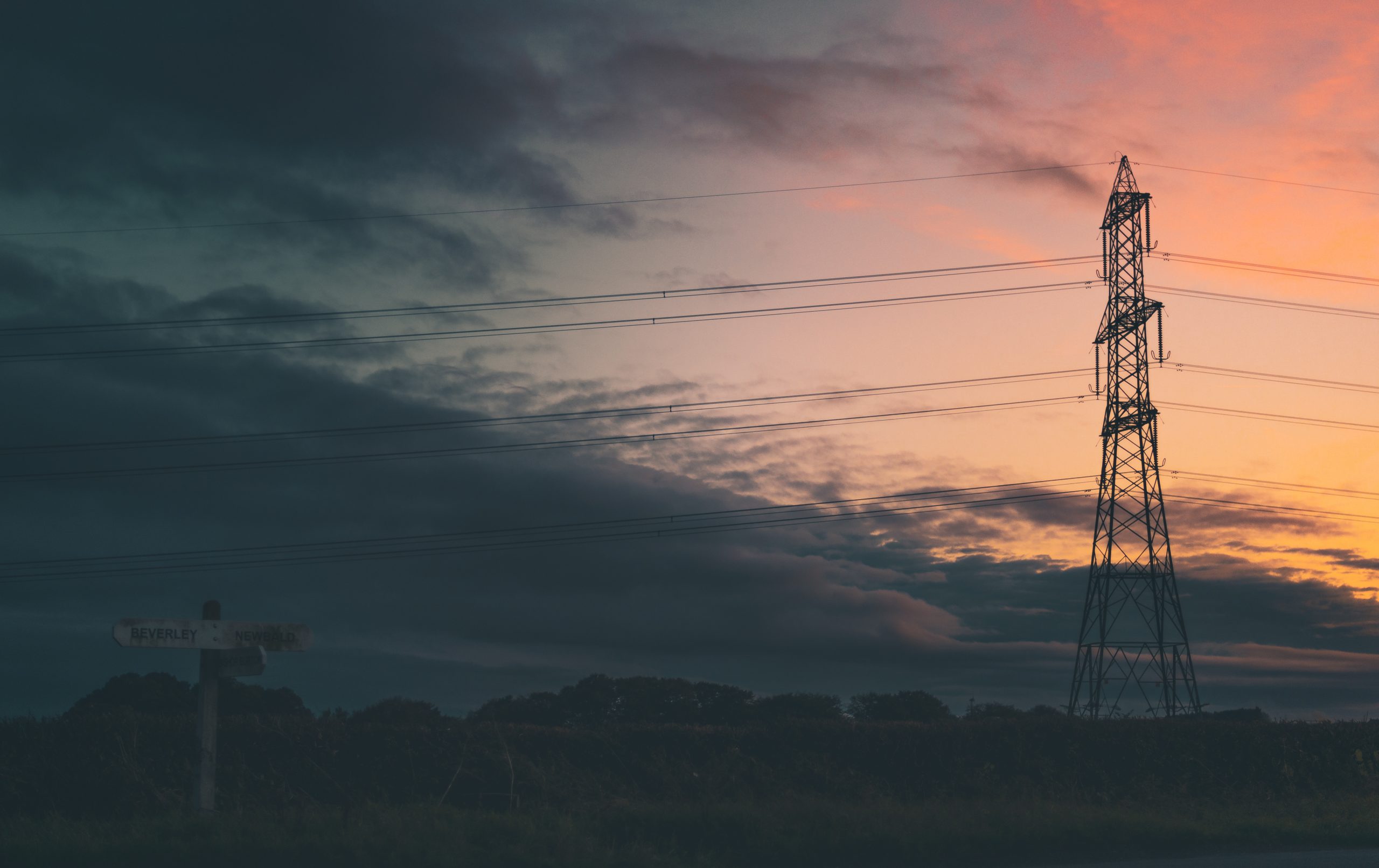
https://www.opusenergy.com/blog/our-contingency-plans-for-coronavirus/
https://www.opusenergy.com/blog/our-contingency-plans-for-coronavirus/
Where does our electricity come from? One answer might be the power stations, wind turbines and solar panels that generate it. You might even go as far as to say the wind, sun, water, biomass and gas powering those stations. Or even the network companies transporting that power around the country. But there’s also a very important middle-man in this process: electricity suppliers.
Most of Great Britain gets its power from one of the ‘Big Six’ energy suppliers, which buy electricity from the wholesale market and then sells it to consumers. However, with more businesses and consumers looking for less carbon-intense electricity sources, there are now a whole host of smaller companies taking on the incumbents and offering all-renewable electricity.
From Ovo to Bulb to Drax’s own Haven Power and Opus Energy, consumers and businesses have more and greener options than ever about where to buy their electricity, with many even offering 100% renewable electricity.
But how do these companies ensure the megawatts powering homes, offices and street lights come from renewable sources?
The electricity we use doesn’t just flow through a single cable from a power station to our houses. It travels through what’s called the transmissions system, which is run by National Grid ESO and local distribution network operators.
Apart from off-grid installations like solar panels on buildings, some of which are unable to export their unused power, all the electricity generated by different sources around the country goes into this same system. It means megawatts generated by a wind turbine get mixed up with those generated by a nuclear reactor or a coal power station.
Think of it as a river. Although it is its own entity, it is fed by multiple streams of water coming from different sources. In the case of electricity, megawatts from various generators are fed into a central system, which then enter homes, offices and devices around the country.
So, what makes green power generated from renewable sources, green power used in homes?
Suppliers can’t control exactly what megawatts you use, but they can influence the makeup of the overall ‘river’ your electricity is pulled from by what electricity they agree to buy and offer to their customers.
Renewable suppliers match the amount of electricity their customers use with the amount they buy from renewable sources. So, if a home uses 4 megawatt-hours (MWh) a year, a supplier will need to ensure it buys an equal amount of power from National Grid, which National Grid sources from generators. If that supplier offers 100% renewable power, it will need to ensure it has the right kinds of deals in place with renewable generators to deliver that amount of power.
It means that while the river of electricity is still a mix from different streams, more of the water will come from renewable streams. Therefore, if more homes and businesses switch to renewable suppliers, more of the overall river will be renewable, which will in turn help to decarbonise the electricity system, enabling a lower-carbon economy.
But how does this fit into the existing electricity business and infrastructure?
But how do suppliers actually buy renewable power from generators?
To understand how suppliers ensure they are buying renewable power you first need to understand how the business works. Or at least, how it used to. The most obvious place to start is with the generators.
Be they gas power stations or an offshore wind farm, the generator is where electricity is produced and are often owned by a supplier.
Suppliers can buy electricity from their own generators, often months or years ahead of delivery. But if there is a shortfall, the supplier can also buy electricity on the wholesale market, where other generators can sell their electricity.
Because suppliers are on a competitive market, their aim is to buy the electricity for the lowest possible price and sell it for more – but at a better rate than rivals. Measures like carbon prices or green incentives help lower the cost of renewable and low-carbon generation, and position it as a more economically viable purchase than more expensive fossil fuels like coal.
Renewable-only suppliers also want to buy electricity as cheap as possible and sell it as affordably as possible. But unlike standard suppliers they only buy electricity from renewable sources.
This can be done by purchasing electricity from independent renewable generators on the wholesale market, or arranged through what are known as Power Purchase Agreements (PPAs) – longer-term contracts between generators and suppliers agreeing on a specific amount of power.
The advantage of these for the renewable generator is it secures revenue for the future, while for the supplier it means a dependable source of electricity. For large installations, these deals are often signed before construction even begins to ensure investors there will be a return.
Transitioning to a low-carbon electricity system, however, is not just about suppliers buying more electricity from renewable sources.
As more businesses, individuals and communities are becoming prosumers and generating their own electricity, the wider role of the supplier in the system is changing.
The government’s feed-in-tariffs financially reward customers for generating their own electricity, even if they don’t export it to the grid. But even small generators can sign deals with suppliers to sell electricity through schemes such as Good Energy’s SmartGen policy, which is open to generators with between 10 and 100 kilowatts (kW) of installed capacity. Similarly Opus Energy helps over 2,100 businesses sell more than 1,100 gigawatt-hours (GWh) of excess wind, solar, anaerobic digestion and hydro power.
For larger prosumer businesses, the relationship with suppliers and the grid is different. Rather than the traditional buying and selling of electricity, it requires a cooperative approach to understand how the prosumer can best utilise their assets.
Beyond increasing the amount of low-carbon electricity, decarbonising the electricity system also means making more efficient use of energy and managing the data that can help improve efficiency. Haven Power’s partnership with Thames Water sees it analyse an average of 68 million half-hour smart meter readings every year, using the data to help the company improve its billing and forecasting. As the wider system becomes more intelligent, suppliers will be able to better forecast how much electricity its customers use and help them reduce their consumption.
The role required of suppliers in a changing system will create opportunities for more renewable and efficient use of electricity. And empower more consumers to get their electricity from low-carbon sources that can help to make the whole country’s electricity greener.
Want a different perspective on the same story? Watch TV’s Jonny Ball explain.
It’s a free and confidential 24-hour service which offers support on anything from financial stress and family and relationship issues to addiction, housing concerns or legal information. There is a phoneline and an app and users can be referred for six sessions of counselling per issue, per year.
Opus Energy ran 15 voluntary workshops to help our leaders understand the benefits of this service and they were attended by 113 managers.
As a result of Opus Energy’s initiative first launched in 2017 to train Mental Health First Aiders, we now have 20 employees qualified to offer a first line of response across the business. They are available to all employees should they would want to speak with a peer about any mental health issues.
A further 16 employees will train as Mental Health First Aiders in 2019.
Opus Energy opened a pop-up juice bar, the Kinetic Café in London, for two days in August. Small business owners were served free energetic juice and welcomed to network and share their business challenges, advice and personal experiences in Q&A sessions.
We served over 1,000 juices to customers and visitors who stopped by the café over the course of two days.
“Different people do things different ways,” says Sam Stocks, an apprentice engineer at Drax Power Station. It’s a sentiment echoed by corporate administration apprentice Chloe Carpenter at Opus Energy. Asked to describe her role, she says, “[It’s] a very different kind of job.”
Chloe and Sam are just two of a number of apprentices at Drax Group who are working across the UK. And while they’re proud to do things differently, they do have something in common – they’re all hands-on, practical people who would rather get stuck in on a project than sit still and hear about it in the classroom.
“I chose an apprenticeship over higher education because I’m more of a doing person,” says Molly Fensome, a corporate administration apprentice. Sam agrees. “I like to be hands-on,” he says. “I don’t like being sat in a classroom.”
They are doing things their way – engineering their own futures while growing personally and professionally. And ensuring the future of our energy supply in the process.
For Sam, working at Drax wasn’t just a sensible career move, it was also following in his family’s footsteps. “My grandad worked in the power station industry all his life. [My family] know exactly what I’m like and they knew what type of place this was to work.”
Drax’s transformation from a coal-powered plant to a modern, sustainable electricity company means Sam’s work is building a power framework for future generations, while also paying homage to his grandad’s career.
Jake Dawson, an electrical engineer apprentice, followed a similar path into the power industry. Being born and bred in the area, Drax Power Station has always been a part of his geography. “Because I’m such a local lad it was perfect for me,” he says.
In his role, Jake can play a key part in the region where he grew up. A recent Oxford Economics report shows that Drax contributes £431 million to Yorkshire and the Humber economy and supports over 3,200 jobs.
Drax is a large organisation, but for Chloe finding role models within her team she can look up to and take guidance from has been easy. “Mentoring sessions are relaxed and you build a special bond with that person,” she says. “You can talk to them about work, outside of work – anything. They’ll always be there for you.”
Corporate administration apprentice Matt Donnelly has had a similar experience, adding that he’s seen his confidence grow, and feels he has made lifelong friends in his role.
Ultimately, it’s not just that they are given the right support, but that apprentices are integrated as a part of the company from day one. “My favourite part of my apprenticeship so far is being part of the team,” says Chloe. “Because you feel like you’re not just an apprentice, but you’re also one of them.”
Sam remembers his first day at Drax Power Station: “It was overwhelming, you don’t actually realise how big it is and realise how many people work here. It’s just normal now, if I go anywhere else, I’m thinking, ‘That’s not as big as at work.’”
It’s not just its size that makes the UK’s biggest single site renewable power station stand out, but the potential for career development there. It’s this that Jake had on his mind when he first made the decision to become an apprentice. He was working in an unskilled job with little opportunity, but he knew he had it in him to find something bigger.
His outlook today as a Drax apprentice is very different. “My aim after the four years is to carry on growing as a person, increasing all my skills that I have, and maybe eventually becoming a supervisor or an engineer, who knows?”
This mindset of striving for better is evident across apprentices. It’s what drove them to join the programme in the first place. “Instead of going somewhere like uni and then possibly coming out without a job, you’ve got a job, and you’re actually learning as you’re doing it,” says Sam. “The skill set that I’ve learnt now – I’ll probably go anywhere in the world with it.”
The UK is undergoing an energy revolution – a transition to a low-carbon economy requiring new energy solutions for power generation, heating, transport and the wider economy. Through our flexible, lower carbon electricity proposition and business to business (B2B) energy solutions, the Group is positioning itself for growth in this environment. More details can be seen on page 4 of our annual report.
Our purpose is to help change the way energy is generated, supplied and used.
Through addressing UK energy needs, and those of our customers, our strategy is designed to deliver growing earnings and cash flow, alongside significant cash returns for shareholders.
Our ambition is to grow our EBITDA to over £425 million by 2025, with over a third of those earnings coming from Pellet Production and B2B Energy Supply to create a broader, more balanced earnings profile. We intend to pay a sustainable and growing dividend to shareholders. Progression towards these targets is underpinned by safety, sustainability, operational excellence and expertise in our markets.
We made significant progress during 2017, but were below our expectations on the challenging scorecard targets we set ourselves in pellet production and biomass availability, the latter reflecting the significant incident we experienced on our biomass rail unloading facilities at the end of 2017, which extended into January 2018. Energy Supply performed well with Opus Energy in line with plan and Haven Power exceeding its targets. Through a combination of this performance and the progress of our strategy we have delivered EBITDA of £229 million, significantly ahead of 2016 (£140 million) and with each of our three businesses contributing positive EBITDA for the first time.
The Group scorecard is reported in full in the Remuneration Report (pp. 81-107 of our annual report) and the KPIs are also shown below. They reflect the diversity of our operations and our need to maintain clear focus on delivering operational excellence.
On a statutory basis we recorded a loss of £151 million, which reflects unrealised losses on derivative contracts, previously announced accounting policy on the accelerated depreciation on coal-specific assets as well as amortisation of newly- acquired intangible assets in Opus Energy. We also calculate underlying earnings, a profit after tax of £2.7 million, which excludes the effect of unrealised gains and losses on derivative contracts and, to assess the performance of the Group without the income statement volatility introduced by non-cash fair value adjustments on our portfolio of forward commodity and currency futures contracts.
During the year we refinanced our existing debt facilities, reducing our debt cost. We also confirmed a new dividend policy which will pay a sustainable and growing dividend (£50 million in respect of 2017), consistent with our commitment to a strong balance sheet and our ambitions for growth. At year end our net debt was £91 million below our 2x net debt to EBITDA target, providing additional headroom. There is more detail on our financial performance in the Group Financial Review on page 46 of our annual report.
In the US, our Pellet Production operations recorded year-on-year growth in output of 35%, with our first two plants now producing at full capacity. During the second half of 2017 we also completed the installation of additional capacity enabling our Morehouse and Amite facilities to handle a greater amount of residue material, supporting efforts to produce good quality pellets at the lowest cost.
As part of our target to expand our biomass self-supply capability we completed the acquisition of LaSalle Bioenergy (LaSalle) adding pellet production capacity. LaSalle commenced commissioning in November 2017 and due to its close proximity to our existing US facilities, once complete, will provide further opportunities for supply chain optimisation.
As in 2016, we benefited from the flexibility of self-supply. This often overlooked attribute of our supply chain enables us to manage biomass supply across the Power Generation business’ planned outage season and to benefit from attractively priced biomass cargoes in the short-term spot market.
In Power Generation, we experienced a significant incident on our biomass rail unloading facilities, including a small fire on a section of conveyor. We fully investigated the incident and following repairs over the Christmas period have now recommissioned the facility, with enhanced operating procedures. This is a timely reminder of the combustible nature of biomass and the need for strong controls and processes to protect our people and assets.
Our biomass units continued to produce high levels of renewable electricity from sustainable wood pellets for the UK market – Drax produced 15% of the UK’s renewable electricity – enough to power Sheffield, Leeds, Liverpool and Manchester combined. In doing so, we are making a vital contribution to the UK’s ambitious targets for decarbonisation across electricity generation, heating and transport – an 80% reduction by 2050 vs. 1990 levels.
We benefited from the first year of operation of our third biomass unit under the Contract for Difference (CfD) scheme which provides an index-linked price for the power produced until March 2027. The unit underwent a major planned outage between September and November, with a full programme of works successfully completed.
The flexibility, reliability and scale of our renewable generation, alongside an attractive total system cost, means we are strongly placed to play a long-term role in the UK’s energy mix. To that end we continue to see long-term biomass generation as a key enabler, allowing the UK Government to meet its decarbonisation targets and the system operator to manage the grid.
The UK Government recently confirmed support for further biomass generation at Drax Power Station and we now plan to continue our work to develop a low-cost solution for a fourth biomass unit, allowing us to provide even more renewable electricity, whilst supporting system stability at minimum cost to the consumer.
Our heritage is coal, but our future is flexible lower-carbon electricity. We are making progress with the development of four new standalone OCGT plants situated in eastern England and Wales and our work to develop options for coal-to-gas repowering with battery technologies. If these options would be supported by 15-year capacity market contracts, providing a clear investment signal and extending visibility of contract-based earnings out to the late 2030s.
In B2B Energy Supply, we completed the acquisition of Opus Energy, a supplier of electricity and gas to corporates and small businesses. The transaction completed in February 2017 and Opus Energy has continued to operate successfully within the Group, achieving its targets and making an immediate and significant contribution to profitability. Alongside this good performance we have also implemented the operational steps necessary to realise further operational benefits of the acquisition, and we now source all of Opus’ power and gas internally.
Haven Power delivered a strong performance with the sale of large volumes of electricity to industrial customers. Through our customer focus and efficiencies, margins have improved and the business generated a positive EBITDA for the first time.
Together, our B2B Energy Supply business now has over 375,000 customer meters, making it the fifth largest B2B power supplier in the UK.
We are delivering innovative low-carbon power solutions, with 46% of our energy sold from renewable sources. As the power system transforms, we will be working closely with our customers to help them adapt to a world of more decentralised and decarbonised power. We see this as a significant opportunity for the Group in the medium to long term.
In October 2017 we completed the sale of Billington Bioenergy (BBE) to Aggregated Micro Power Holding (AMPH). Consideration for the transaction was £2.3 million, comprised of £1.6 million of shares in AMPH and £0.7 million of cash.
The sale of BBE is aligned with our strategy to focus on B2B energy supply. However, through our shareholding in AMPH, we will retain an interest in the UK heating market, whilst gaining exposure to the development of small-scale distributed energy assets.
We continue to operate in a changing environment. The full impact of the UK’s decision to leave the EU is still unknown.
The immediate impact on the Group was a weakening of Sterling and an associated increase in the cost of biomass, which is generally denominated in other currencies. Through our utilisation of medium-term foreign exchange hedges the Group protected the cash impact of this weakness. In 2017, Sterling has generally strengthened, and we have been able to extend our hedged position out to 2022 at rates close to those that we saw before Brexit.
In terms of UK energy policy, the Government’s main focus has been on what it sees as unfair treatment of domestic consumers on legacy standard variable tariff (SVT) contracts. SVT are not a common feature of the B2B market. At the microbusiness end of this market, which is closer in size to domestic, most of our customers are on fixed price products and are active in renewing contracts.
The UK Government’s response to its consultation on the cessation of coal generation by 2025 has confirmed an end to non-compliant coal generation by October 2025.
We believe our assets, projects and ability to support our customers’ electricity management will support the Government’s ambition to maintain reliability when coal generation ceases.
Running a resilient, reliable grid is not simply about meeting the power demand on the system; there are also system support services which are essential to its effective operation. As the grid decentralises and becomes dependent on smaller, distributed generation, the number of plants able to provide these services is reducing. Biomass generation, our proposed OCGTs and our repowering project would allow us to meet these needs, but this will not come for free. A reliable, flexible, low-carbon energy system will require the right long-term incentives.
In November 2017, the Government confirmed that the UK will maintain a total carbon price (the combined UK Carbon Price Support – CPS – and the European Union Emissions Trading Scheme – EU ETS) at around the current level. CPS has been the single most effective instrument in reducing the level of carbon emissions in generation and we continue to support the pricing of carbon, a view echoed in a report prepared for the UK Government by the leading academic Professor Dieter Helm.
Against this backdrop we continue to make an important contribution to the UK economy. According to a study published by Oxford Economics in 2016, Drax’s total economic impact – including our supply chain and the wages our employees and suppliers’ employees spend in the wider consumer-economy was £1.7 billion, supporting 18,500 jobs across the UK.
The health, safety and wellbeing of our employees and contractors is vital to the Group, with safety at the centre of our operational philosophy. We also recognise the growing need to support the wellbeing of our employees and their mental health.
During the year we continued to use Total Recordable Injury Rate (TRIR) as our primary KPI in this area. Performance was positive, at 0.27, but we expect this to improve in the coming year.
The incident at our biomass rail unloading facilities in December did not lead to physical injuries but was nonetheless a significant event and caused disruption into 2018.
We consequently launched an incident investigation to ensure our personal and process safety management procedures are robust.
To promote greater awareness around wellbeing we have embedded this in our new people strategy and expect to focus more energy and resources on this important area during 2018.
Strong corporate governance is at the heart of the Group – acting responsibly, doing the right thing and being transparent. As the Group grows the range of sustainability issues we face is widening and recognising the importance of strong corporate governance, we have published a comprehensive overview of our sustainability progress in 2017 on our website. This also highlights future priorities to broaden our approach to sustainability and improved reporting of environment, social and governance (ESG) performance. We have also completed the process which allows us to participate in the UN Global Compact (UNGC) – an international framework which will guide our approach in the areas of human rights, labour, environment and anti-corruption.
During 2017 we published our first statement on the prevention of slavery and human trafficking in compliance with the UK Modern Slavery Act. We have added modern slavery awareness to our programme of regular training for contract managers and reviewed our counterparty due diligence processes.
We have continued to maintain our rigorous and robust approach to biomass sustainability, ensuring the wood pellets we use are sustainable, low-carbon and fully compliant with the UK’s mandatory sustainability standards for biomass. The biomass we use to generate electricity provides a 64% carbon emissions saving against gas, inclusive of supply chain emissions. Our biomass lifecycle carbon emissions are 36g CO2 / MJ, less than half the UK Government’s 79g CO2 / MJ limit.
Our people are a key asset of the business. Through 2017 we developed a new people strategy. The strategy focuses on driving performance and developing talent to deliver the Group’s objectives. We have established Group-wide practices, including a career development and behaviour framework focused on performance and personal development.
A key part of our strategy is to identify opportunities to improve existing operations and create options for long-term growth. To that end we have established a dedicated Research and Innovation (R&I) team led by the Drax engineers who delivered our world-first biomass generation and supply chain solution.
We are actively looking at ways to improve the efficiency of our operations, notably in our biomass supply chain.
Biomass is our largest single cost and as such we are focused on greater supply chain efficiency and the extraction of value from a wide range of low-value residue materials.
In B2B Energy Supply we are using our engineering expertise to help offer our customers value-adding services and products which will improve efficiency and allow them to optimise their energy consumption.
In the following sections we review the performance of our businesses during the year.
Our pellets provide a sustainable, low-carbon fuel source – one that can be safely and efficiently delivered through our global supply chain and used by Drax’s Power Generation business to make renewable electricity for the UK. Our manufacturing operations also promote forest health by incentivising local landowners to actively manage and reinvest in their forests.
Safety remains our primary concern and we have delivered year-on-year reduction in the level of recordable incidents.
Output at our Amite and Morehouse pellet plants increased significantly, although was below our target for the year.
We have remained focused on opportunities to improve efficiencies and capture cost savings as part of our drive to produce good quality pellets at the lowest possible cost. We still have more work to do in this area to optimise quality and cost, as our performance was below target for the year.
As part of our plans to optimise and improve operations we added 150k tonnes capacity at our existing plants, bringing total installed capacity to 1.1 million tonnes and increasing the amount of lower cost sawmill residues we are able to process and used in our pellets.
By-products of higher value wood industries, such as sawdust from sawmills, offer a low-cost source of residues for use in our pellet production process and during 2017 we added an additional 150k tonnes of capacity at our pellet plants to allow us to use more of this material. By investing in giant hydraulic platforms known as ‘truck dumps’, operators at Amite and Morehouse can unload a 50-foot truck carrying either sawdust or wood chips and weighing 60 tonnes in less than two minutes, increasing processing capacity, reducing the cost of processing and increasing the use of lower cost residues.
Find out more: www.drax.com/truckdumps and www.drax.com/sustainability/sourcing
At our Baton Rouge port facility greater volumes of production from our facilities drove higher levels of throughput with 17 vessels loaded and dispatched during the year (2016: 11 vessels).
In April, in line with our strategy to increase self-supply, we acquired a 450k tonne wood pellet plant – LaSalle Bioenergy (LaSalle). Commissioning of the plant began in November 2017 and we expect to increase production through 2018. LaSalle is within a 200-mile radius of our existing facilities. By leveraging the locational benefits of these assets we aim to deliver further operational and financial efficiencies.
The location of our operations allows us to leverage benefits of multiple assets and locations for operational efficiencies
All sites within 200-mile radius
Operational efficiencies
Shared logistics to Baton Rouge
Complementary fibre sourcing
Find out more: www.draxbiomass.com
There was a significant improvement in 2017, with EBITDA of £5.5 million (2016: £6.3 million negative EBITDA), driven by increasing volumes of wood pellets produced and sold to the Power Generation business. Sales of pellets in the year ending 31 December 2017 totalled £136 million, an increase of 84% over 2016.
Gross margin increased, reflecting higher production volumes. Raw fibre procurement, transportation and processing comprised the majority of cost of sales and as such this remains an important area of focus and an opportunity for the business. Through incremental investment in plant enhancements we expect to see further benefits from efficiencies and greater utilisation of lower cost residues.
Total operating costs have increased, reflecting an increase in operations at Amite, Morehouse and the Port of Baton Rouge, alongside the addition of LaSalle.
We acquired LaSalle for $35 million and have invested an additional $27 million as part of a programme to return the unit to service.
2017 £m | 2016 £m |
|
---|---|---|
Revenue | 135.7 | 73.6 |
Cost of sales | (96.7) | (55.5) |
Gross profit | 39.0 | 18.1 |
Operating costs | (33.5) | (24.4) |
EBITDA | 5.5 | (6.3) |
Area | KPI | Unit of measure | 2017 | 2016 |
---|---|---|---|---|
Operations | Fines at disport | % | 9.6 | 7.6 |
Operations | Output | ,000 tonnes | 822 | 607 |
Financial | Variable cost/tonne | $/tonne | 77 | 82 |
Through 2018 we expect to continue to deliver growth in EBITDA from our existing assets. Our focus is on the commissioning of LaSalle alongside opportunities for optimisation and efficiencies in our processes, to deliver good quality pellets at the lowest cost.
We remain alert to market opportunities to develop further capacity as part of our self-supply strategy.
Drax Power Station remains the largest power station in the UK (almost twice the size of the next largest). During the year the station met 6% of the UK’s electricity needs, whilst providing 15% of its renewable electricity, alongside important system support services.
With an increase in intermittent renewables and a reduction in the responsive thermal generation historically provided by coal, the system of the future will require capacity which is reliable, flexible and able to respond quickly to changes in system demand and provide system support services. These long-term needs inform our biomass generation and the development of options for investment in gas – Open Cycle Gas Turbines (OCGTs) and coal-to-gas repowering.
We are developing options for four new OCGT gas power stations, two of which already have planning permission and could be on the system in the early 2020s, subject to being awarded a capacity agreement.
A high-tech new control room at Drax Power Station will allow engineers to have real time remote control of our OCGT assets via a fibre-optic cable network. Able to fire up from cold and produce power in minutes rather than hours, our OCGTs will help maintain system security as intermittent renewable sources of power increase and older thermal plants close.
Investment case
Find out more: www.drax.com/about-us/#our-projects
In October the Government published its Clean Growth Plan, setting out its plans for delivery of its legally binding target to reduce 2050 carbon emissions by 80% versus 1990 levels across electricity generation, heating and transport. This reinforces the Drax proposition – flexible, reliable, low-carbon electricity.
In November the Government updated its intentions regarding the future trajectory of UK Carbon Price Support (CPS), indicating that the total cost of carbon tax in the UK (the total of CPS and the EU Emissions Trading Scheme) would continue at around the current level (the tax is currently set at £18/tonne) whilst coal remains on the system.
We believe that CPS has been the single most effective instrument in reducing carbon emissions from generation and that having an appropriate price for carbon emissions is the right way to provide a market signal to further reduce emissions in support of the UK’s long-term decarbonisation targets.
The UK Government has now confirmed an end to non-compliant coal generation by 2025. We support this move subject to an appropriate alternative technology being in place. With this in mind we have continued to develop options for our remaining coal assets to convert to biomass or gas, to provide the reliable, flexible capacity which we believe will be required to manage the increasingly volatile energy system of the future.
Most recently with confirmation of Government support for further biomass generation at Drax Power Station we plan to continue our work to develop a low-cost solution for a fourth biomass unit, accelerating the removal of coal-fired generation from the UK electricity system, whilst supporting security of supply.
2017 saw the first full year of operation of our biomass unit under the Contract for Difference (CfD) mechanism, which provides index-linked revenues for renewable electricity out to 2027.
Our other biomass units are supported by the Renewable Obligation Certificate (ROC) mechanism which, similar to the CfD, is also index-linked to 2027. This acts as a premium above the price of power we sell from these units. We sell power forward to the extent there is liquidity in the power markets which, combined with our fuel hedging strategy, provides long-term earnings and revenue visibility.
Lower gas prices, higher carbon costs and the continued penetration of intermittent renewables have kept wholesale electricity prices subdued.
With increasing levels of intermittent renewables we are continuing to see opportunities to extract value from flexibility – short-term power and balancing market activity, the provision of Ancillary Services and the value achieved from out-of-specification fuels. To capture value in this market we continue to focus resource on optimising availability and flexibility of both coal and biomass units. This whole process requires a high level of teamwork between the operational and commercial teams across the Group to capture and protect value.
Over the period 2017 to 2022 we expect to earn £90 million from a series of one-year capacity market contracts for our coal units, demonstrating that they still have a role to play. The first of these contracts commenced in October 2017, adding £3 million to EBITDA.
Lastly, we continue to source attractively priced fuel cargoes – out-of-specification coals and distressed cargoes, which help keep costs down for the business and consumers. We do this for both coal and biomass. This is a good example of how our commercial and operational teams work together to identify opportunities to create value for the business, as these fuels typically require more complex handling processes.
You can follow the market and see prices at electricinsights.co.uk
Options for Drax Power Station to operate into the late 2030s and beyond moved up a gear in 2017 with the development of an option to repower two coal units to gas. Drax gave notice of the nationally significant infrastructure project to the Planning Inspectorate in September 2017. One of the units could be eligible for the capacity market auction planned for December 2019.
Local community consultations began in November 2017 and continued in February 2018 on options including up to 3.6GW of new gas generation capacity, a gas pipeline and 200MW of battery storage in line with Government plans to end non-compliant coal generation by 2025 and Drax Group’s strategy of playing a vital role in the future energy system.
Find out more: repower.drax.com
Overall, we delivered a good performance during 2017 and maintained a strong safety performance.
We completed a major planned outage on the unit supported by the CfD contract. This unit provides stable and reliable baseload renewable electricity to the network and long-term earnings visibility for the Group. The safe and efficient completion of these complex works is a credit to those involved and reflects our continued focus on opportunities for improvement and efficiencies.
The entire organisation has responded to a number of challenging unplanned events. Most notably, in December we experienced a fire on a section of conveyor at our biomass rail unloading facility and consequently an unplanned outage from late December 2017 to mid-January 2018. Following investigation and recommissioning, the facility has returned to service with enhanced operating procedures. Although this issue did not relate to the operation of the biomass-generating units, the resulting restriction on fuel deliveries by rail required the optimisation of generation across our biomass units, resulting in lower EBITDA and full year biomass availability than our target for the year.
Financial performance has significantly improved, with EBITDA of £238 million (2016: £174 million), principally due to the CfD mechanism.
Value from flexibility was below our target for the year, principally reflecting a lower level of Ancillary Service payments versus 2016.
Our operational performance drives the results. The financial impact of the unplanned outage on the rail unloading facility was mitigated by optimisation of our available biomass and the use of additional generation capacity retained for self-insurance purposes. However, this incident is a reminder of the need to invest appropriately to maintain a high level of operational availability and flexibility.
At the operating cost level, we have reduced costs reflecting the efficient single outage and our focus on the implementation of lean management techniques.
2017 £m | 2016 £m |
|
---|---|---|
Revenue | 2,719.6 | 2,490.9 |
Cost of power purchases | (891.2) | (904.4) |
Grid charges | (62.9) | (69.4) |
Fuel and other costs | (1,367.1) | (1,180.1) |
Cost of sales | (2,321.2) | (2,153.9) |
Gross profit | 398.4 | 337.0 |
Operating costs | (160.9) | (163.2) |
EBITDA | 237.5 | 173.8 |
Area | KPI | Unit of measure | 2017 | 2016 |
---|---|---|---|---|
Operations | Biomass unit technical availability | % | Below target | Below target |
Operations | Value from flexibility | £m | 88 | N/A |
We aim to optimise returns from our core assets, through reliable, flexible, low-carbon energy solutions which provide a long-term solution to the UK’s energy needs. Alongside this, value in the generation market will be created from an ability to execute agile decisions and capture value from volatile short-term power markets.
We will also continue to explore opportunities for lower carbon generation, to exploit our strengths and create opportunities for the long term. To that end we will continue to develop options for gas and pursue efficiencies through our biomass supply chain.
Our B2B Energy Supply business – comprised of Opus Energy and Haven Power – is the fifth largest B2B power supplier in the UK. As the power system transforms, we will be working closely with our customers to help them adapt to a world of more decentralised and decarbonised power. The key factors influencing our business are regulation, competition and our operational performance.
The UK Government’s main focus has been on what it sees as unfair treatment of domestic consumers on legacy standard variable tariff (SVT) contracts. The Government will take forward legislation which will provide the regulator Ofgem with the authority to cap these domestic tariffs. SVTs are not a feature of our business. Our focus remains on the B2B market. At the microbusiness end of the market, which is closer in proximity to domestic, most of our customers are on fixed price products and are actively rather than passively renewing their power supply contracts.
The B2B market remains competitive with 65 different suppliers across the market. Our Haven Power and Opus Energy businesses offer customer-centric power, gas and services. We offer simplicity and flexibility across our products and actively engage with customers to help them manage their energy requirements and reduce carbon emissions.
90% of the electricity that Opus Energy supplied last year came from clean, renewable sources, at no extra cost to their predominantly small and medium-sized business customers. For those customers who want it, 100% renewable energy contracts are also available.
This was exactly what All Saints Church in Ascot was looking for to power their business.
Assistant Church Warden, Chris Gunton, commented:
“We wanted to move to a greener energy supplier, without paying a premium, so approached an energy broker for guidance. They advised us that Opus Energy were a reliable company with a good reputation, and when we asked for a quote they were the most competitive.”
It was a similar story for the Salisbury Museum, in Wiltshire. Nicola Kilgour-Croft, Finance Manager, said:
“We were looking for an energy supplier that offered great value, combined with the right length of contract and good ethics. Opus Energy ticked all these boxes for us.”
Alongside supplying customers, Opus Energy has Power Purchase Agreements with over 2,300 independent UK renewable energy generators. These could be anything from a single wind turbine owned by a village community, to Europe’s greenest zoo, Hamerton Zoo Park.
Commented Andrew Swales, Director of Hamerton Zoo:
“Working with Opus Energy has given us competitive prices, considerably better documentation and a highly efficient service. We’d happily recommend them.”
We have remained focused on delivering an excellent standard of customer service, which is central to our proposition.
February 2017 saw the completion of the acquisition of Opus Energy, which has made good progress integrating into the Group supported by a dedicated team, who have been working on systems, people and commercial projects to ensure our processes work effectively together.
In March we completed the purchase of a new office facility in Northampton, enabling the consolidation of four Opus Energy offices into one and the centralisation of the operational teams.
Sales volumes at Opus Energy were lower than target, reflecting our focus on margin which has remained strong and customer renewal rates were towards the high end of expectation. This reflects the continued commitment to a strong level of customer service and in recognition of this Opus Energy was awarded Utility Provider to Small Businesses of the Year 2017 at the British Business Awards.
At Haven Power we have continued to focus on value-adding flexible products and services particularly to Industrial & Commercial customers whose needs extend beyond commodity supply.
This is demonstrated through our ability to help customers manage and optimise their power consumption profiles through collaboration with our carefully selected partners. Through better systems and services, customer targeting and a keener focus on cost to serve we are driving efficiencies and improved margin at Haven Power.
Following the acquisition of Opus Energy the major Enterprise Resource Platform (ERP) system upgrade was re-planned which has led to a revised timeline from Q2 2018 onwards.
We continue to actively manage credit risk by assessing the financial strength of customers and applying rigorous credit management processes, with a strong focus continuing to be placed on billing and cash collection.
Health and safety remains an area of focus for the business and we continue to target a reduction in the level of recordable incidents.
Financial performance has significantly improved, with EBITDA of £29 million in line with our guidance (2016: £4 million negative). This was principally due to the acquisition of Opus Energy, which added 10 months of EBITDA, but also improved financial performance from Haven Power, which was ahead of plan.
Third Party Costs (TPCs) include grid charges, the cost of meeting our obligations under the Renewable Obligation (RO) and small-scale Feed-in-Tariff schemes. Grid charges include distribution, transmission and system balancing costs. TPCs have continued to increase and now account for 50% of revenue.
Total operating costs have risen with the acquisition of Opus Energy. We remain confident that over time the benefits of common platforms and knowledge sharing will lead to efficiencies.
2017 £m | 2016 £m |
|
---|---|---|
Revenue | 1,999.0 | 1,326.4 |
Cost of power purchases | (883.7) | (688.9) |
Grid charges | (435.8) | (310.4) |
Other retail costs | (562.1) | (303.6) |
Cost of sales | (1,881.6) | (1,302.9) |
Gross profit | 117.4 | 23.5 |
Operating costs | (88.0) | (27.8) |
EBITDA | 29.4 | (4.3) |
Area | KPI | Unit of measure | 2017 | 2016 |
---|---|---|---|---|
Operations | Implementation of new ERP (Haven Power) | Date | Q2 2018 | N/A |
Operations | Sales volume (Opus Energy) | TWh | 5.7 | N/A |
Operations | Renewal rate (Opus Energy) | % | Above Target | N/A |
In 2018 we will focus on Opus Energy on-boarding, systems development and the roll out of smart meters.
We continue to see opportunities for EBITDA growth in the B2B markets, which we will deliver through our customer-focused supply proposition.
Our focus in 2018 remains on the delivery of our strategy and long-term ambitions for earnings growth, underpinned by safety, sustainability, operational excellence and expertise in our markets. We also recognise that being the most efficient operator in each of our markets is a key factor in our success.
Our objective in Pellet Production remains the commissioning of LaSalle, the production of good quality pellets at the lowest cost, cross-supply chain optimisation and identifying attractive options to increase self-supply.
Our biomass proposition is strong – reliable, flexible, low-carbon renewable electricity and system support which, combined with an effective fuel hedging strategy, will provide long-term earnings visibility. We remain focused on ways to increase supply chain efficiency and make biomass competitive beyond 2027. As part of this we remain focused on the optimisation of our assets in the US Gulf and reduction in pellet cost. To support this focus we are moving our US headquarters from Atlanta to Monroe, Louisiana, which benefits from a much closer proximity to these assets.
In Power Generation, we continue to explore ways to optimise our existing operations, whilst meeting the needs of the changing UK electricity system.
We remain supportive of the UK Government’s decarbonisation targets and will continue our work to deliver four OCGTs and a low-cost biomass unit conversion utilising existing infrastructure at Drax Power Station, alongside developing the option to repowering the remaining coal units to gas.
In B2B Energy Supply, we will continue to grow our B2B offering, with significant opportunities to grow market share. At the same time, we will invest in supporting infrastructure to ensure we can continue to grow, offer market-leading digital propositions and smart metering services.
Pellet Production
Power Generation
B2B Energy Supply
We have made good progress on the delivery of our strategy and will continue to build on this as we progress our targets for 2025, whilst playing an important role in our markets and helping to change the way energy is generated, supplied and used.
Gamlingay Community Turbine is situated just outside the village of Gamlingay, Cambridgeshire. It is an enterprise privately funded by local residents and businesses. The village installed the turbine for three reasons: to reduce its carbon footprint; to raise money for the community by selling the turbine’s power; and to create a good investment opportunity for individuals and businesses in the area.
Opus Energy offers to purchase power at market-leading prices. The team behind the Community Turbine were seeking a high level of customer service, which is why they chose to sell their power to Opus Energy. Mr Brettle, a director of the project, comments:
“It really came down to how easy it was to talk to Opus Energy. We’re all people with day jobs so don’t have much spare time, and we’re certainly not experts in this area! Opus Energy helped us cut through the jargon and gave us confidence that nothing horrible will happen because we’d missed some technical detail. They made the entire process simple from start to finish.”
Gamlingay Community Turbine Ltd will give 10% of the net income, after all running costs, to a community fund. This will enable them to create a long-term income stream for the local area which will be used to support environmentally friendly projects for the benefit of the whole community.
Our B2B Energy Supply business offers personal account management to our large corporate customers and our employees strive to support customers at every step. We aim to treat customers fairly at all times and commit to being professional, honest and transparent in our interactions.
Both Haven Power and Opus Energy have strict standards, outlined publicly in their respective “treating customers fairly” policies. The statements explain how we communicate with customers, transfer their supply, deal with billing and payment and how we handle complaints. Opus Energy publishes an additional performance standard confirming its commitment to customers. Employees receive regular training on providing a high level of customer service.
When things do go wrong, we are quick to make amends and resolve issues efficiently. We have publicly available complaints procedures and make it clear who to contact. At Opus Energy, complaints are overseen by the Customer Experience Board.
We are proud of the recognition both Haven Power and Opus Energy received for their dedication to customer service in 2017. Haven Power was shortlisted for “Supplier of the Year” at the Energy Awards 2017 and named the UK’s best performing energy supplier by Third Party Intermediaries (TPIs) in this year’s Cornwall Insight Report. Opus Energy won “Utilities Provider of the Year” at the British Small Business Awards 2017 and was shortlisted in the National Business Awards 2017.
We take the privacy and security of our customers’ data seriously. We are committed to maintaining effective and sustainable privacy and security programmes dedicated to ensuring our customers have confidence in our data handling practices.
As part of our commitment in this area, we appointed a Group Data Protection Officer to enhance our privacy compliance. We are in the process of updating our Privacy Compliance Programme to take account of new requirements of the General Data Protection Regulation (GDPR), enforceable in May 2018, and other associated new data protection legislation.
To support our privacy compliance process and organisation policies, we undertook an extensive technical Security Improvement Programme. We implemented industry-leading control measures to protect our customer and employee data by detecting and preventing threats and security breaches.
Programme initiatives included information protection, using protection technology to automatically detect personally identifiable information and protect it from unauthorised access and disclosure. In addition, advanced threat monitoring and analytics measures implemented mean we have layered toolsets designed to detect, identify, respond to and resolve cyber threats and attacks before they can happen.
Founded in 1860, Salisbury Museum is located in a Grade I listed building opposite Salisbury Cathedral. As a charitable, not-for-profit organisation, the museum relies on entry fees, grants, donations and the support of its members to continue its vital work. Finding a business energy supplier that offered the best prices on the market, as well as the right length of contract and good ethics, was important for the museum.
SMEs are a key part of Opus Energy’s business and they know that a business energy service that is as smooth and efficient as possible is a top priority.
Nicola Kilgour-Croft, Finance Manager at Salisbury Museum, commented:
“The switching process went through really smoothly, and the facility to receive invoices via email means I don’t need to spend time on the phone trying to sort out payment. Having 12-month contracts really works for us.
“We were looking for a business energy supplier that offered great value, combined with the right length of contract and good ethics – and Opus Energy ticked all these boxes for us.”
Whether powering homes across Britain or helping stabilise the national grid, Drax Power Station’s impact to our electricity network is far reaching. But it doesn’t stop at generating and supplying power.
A new report by Oxford Economics, commissioned by Drax, has found that in addition to its important role powering Britain, Drax Group also provides an economic boost to areas across the country.
Here are three ways Drax Group contributed to the UK economy in 2016.
Drax Group contributed an estimated £1.67 billion to UK gross domestic product (GDP) in 2016, an increase from £1.24 billion in 2015. Of that figure, £301 million was added directly – as a result of the group’s own activities such as the generating and selling of power.
And while this is an impressive 6.1% increase on 2015, the numbers are even more significant when looking at the benefit beyond the group’s core activities.
In 2016, Drax Group’s spending with external suppliers such as rail freight wagon manufacturer WH Davis and IMServ, which supplies Automated Meter Reading technology to Opus Energy, reached £872 million. A further £36m was spent by these suppliers across their own supply chain to help them provide their services to Drax.
There is an even greater impact when considering how this money filters through employees and suppliers into local retail, leisure and service economies. Something which is especially important when the number of jobs Drax supports is taken into account.
Drax Group directly employed more than 2,000 people in 2016, but across the country it supports far more – 18,500, a significant increase from the 14,150 of 2015.
These jobs are primarily in high-skilled manufacturing, engineering, construction, IT, professional business services and transport. While 3,650 of these were in Drax Power Station’s native Yorkshire and Humber area, this year saw the group’s overall impact extend much further.
Roughly a quarter (£419 million) of Drax’s total contribution to UK GDP was generated in the Yorkshire and the Humber region. When the North West and North East were included, the company impacted the northern economy to the tune of £577m and supported over 6,000 jobs.
Yorkshire and the Humber was closely followed by the East of England, the home of Haven Power, which saw the second highest impact – registering more than £200 million contributed in GVA – and London and the East Midlands.
This is thanks in part to the growing activities of Drax Group companies. Both Haven Power and Opus Energy (which became a part of Drax Group in February 2017), are helping the UK move towards a low carbon future by supplying an increasing amount of British companies with renewable power. With offices in Ipswich, Oxford, Northampton and Cardiff, Haven Power and Opus Energy highlight how Drax Group businesses are direct drivers for local GDP and employment. Opus Energy supported 1,600 jobs and £130 million in GVA in Wales, while Haven Power contributed £232 million to the East of England.
These numbers are noteworthy, but what makes them all the more significant is how this translates into tax revenue. Operations at Drax Group generated an estimated £327 million for the UK’s public purse – equivalent to the salaries of almost 14,000 nurses or 11,900 teachers.
As the group continues to grow – adding new power generation assets to the national electricity transmission system and helping more businesses use renewable power – Drax can increase its positive impact on the UK’s economy and help to make the country’s low-carbon future a reality more quickly.
To find out more about how Drax has benefited the UK’s economy, visit draximpact.co.uk. The full 2016 report can be downloaded here. Interested in a career at Drax Group? Please visit Careers to find out more.