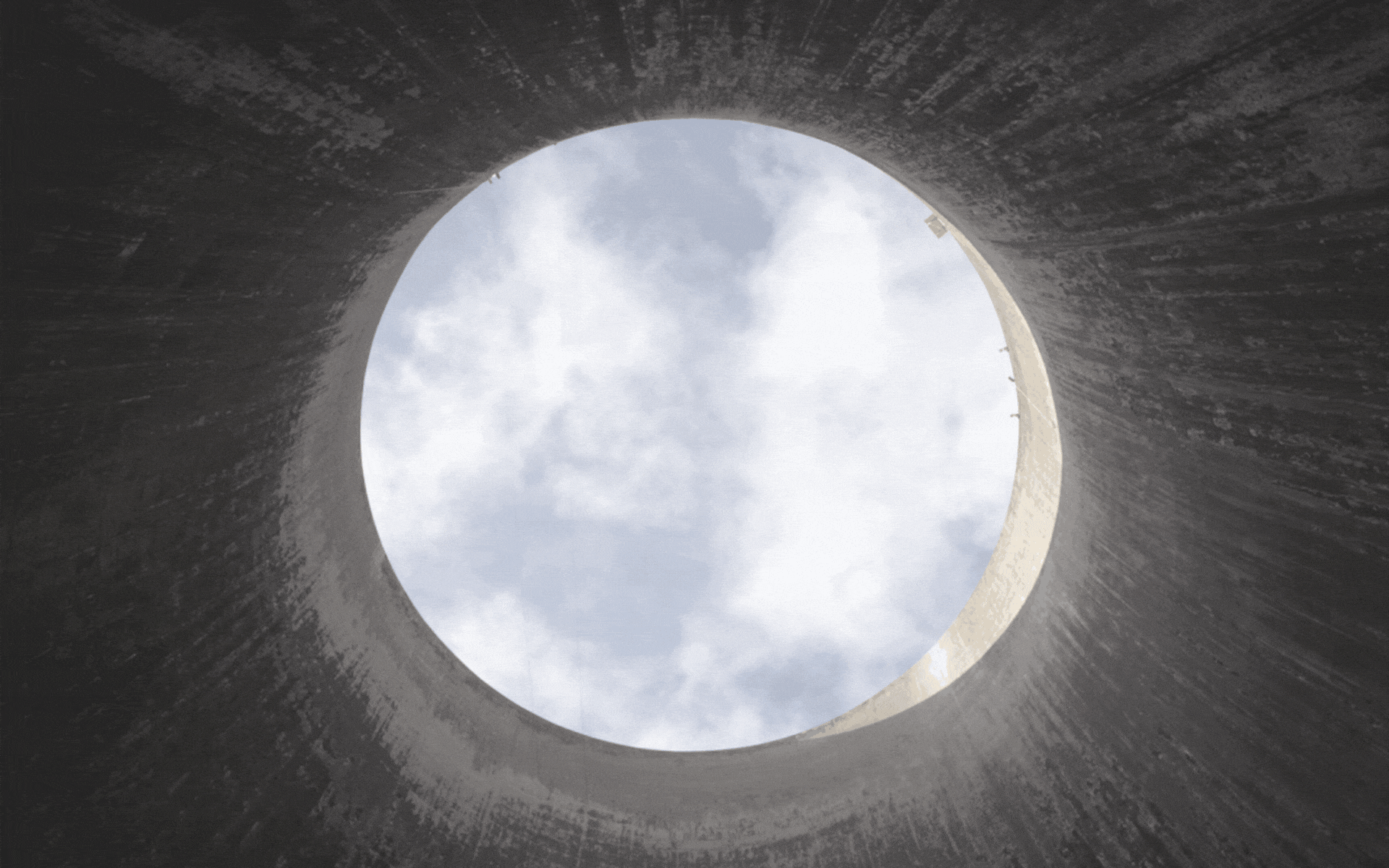
The silhouette of cooling towers on the horizon is one of the most recognisable symbols of electricity generation around the world. But inside these massive structures is an environment unlike any other.
When cooling towers are in operation, torrents of warm water cascade down to a huge pond at its base, the air cooling it as it falls. Plumes of water vapour rise through the structure and into the air.
But when shut down – for maintenance, for example – the inside of a cooling tower is a very different place. The vast emptiness of the space can be eerily silent. Even the smallest noise echoes around its concrete shell.
Standing at over 114 metres high, each of Drax’s 12 cooling towers are 86 metres in diameter at their base, 53 metres at their summit, and could comfortably fit the Statue of Liberty inside. Everything about them is huge, but they are not the unsophisticated masses of concrete they appear from afar.
“Look at a cooling tower and you might think it’s a substantial, thick structure. It’s not,” explains Nick Smith, a civil engineer at Drax. “It’s basically like an egg shell. It is the shape that gives it its strength.” For the majority of their height, a typical cooling tower is between just 178 and 180 mm – or 7 inches – thick.
It’s a testament to the original design and construction that they require such limited maintenance more than half a century after plans were first drawn up. Especially considering they are in daily use.
What does a cooling tower do?
Water is an essential part of thermal electricity generation. It is turned into high-pressure steam in the extreme temperatures of a boiler before being used to spin turbines and generate electricity. Water within the boiler is ‘de-mineralised’ and purified to prevent damage to the turbine blades and infrastructure.
Once it leaves the turbine, the steam is cooled to pure water again in the condenser so it can be reused in the boiler. To do this the steam is passed over pipes containing cold water from the cooling towers, which cools and condenses the steam while also heating up the cold water to roughly 40 degrees Celsius, the temperature it is at when it enters the cooling tower.
Inside the towers the warm water is poured over what’s known as the cooling tower pack, a series of stacks of corrugated plastic that sit roughly 30 metres up the tower. The heat and the tower’s height create a natural draught. This pulls air in from the cavities at the base of the tower – called the throat – which cools the water to around 20°C as it cascades down the stack into a pond below. It is then returned to the condenser where the cooling cycle starts all over again.
Only around 2% of the water escapes through the top of the cooling towers as water vapour – which is what can be seen exiting the top of the towers – with a further 1% returned to the River Ouse to control water levels. These small losses are replenished with water taken from the Ouse. It highlights the genius of the towers’ design that their shape alone can cool water so efficiently on an industrial scale with minimal environmental impact.
A lasting design
A cooling tower’s iconic shape is known as a hyperboloid, referring to its inward curve. This makes them very stable, but to make them strong enough to last as long as they have, Drax’s cooling towers have the added assistance of reinforced concrete.
“Concrete is very strong in compression, but it has hardly any tensile strength,” says Smith. “Therefore our cooling towers have both vertical and horizontal hoop reinforcement to take any tensile forces generated. It is the concrete and steel working together that gives the reinforced concrete its strength.”
The level of design and engineering of Drax’s cooling towers are all the more impressive considering their age. “The construction of our first tower was completed in 1970 and designed in the mid 1960s,” says Smith, pointing out, “they were designed at a time where there wasn’t huge computing processing power, so they would likely have been designed by hand.”
“They were constructed to a very high degree of accuracy even when a lot of the equipment used would have been manual,” he adds.
Designing and building a cooling tower today, he adds, would require significant computing power and sophisticated setting-out equipment to ensure the accuracy of the construction. However, the underlying principles of the towers’ shape and how well they have continued to perform since their construction would give little reason to deviate from the current design.
In fact, that consistent performance means that even as the nature of generating electricity develops to include new fuels and technologies, cooling towers remain an integral part of the process. Drax’s Repower project– which could see the conversion of the plant’s remaining coal units to gas and the installation of a giant battery facility – is a significant step forward in the evolution of power generation, yet the design and purpose of the cooling towers would remain the same.
The structures that will shape the landscape of the future of electricity generation may include wind turbines, biomass domes and solar panels. But the enduring functionality of natural draught concrete cooling towers means they will still play a role in producing the country’s electricity – even as generation diversifies.