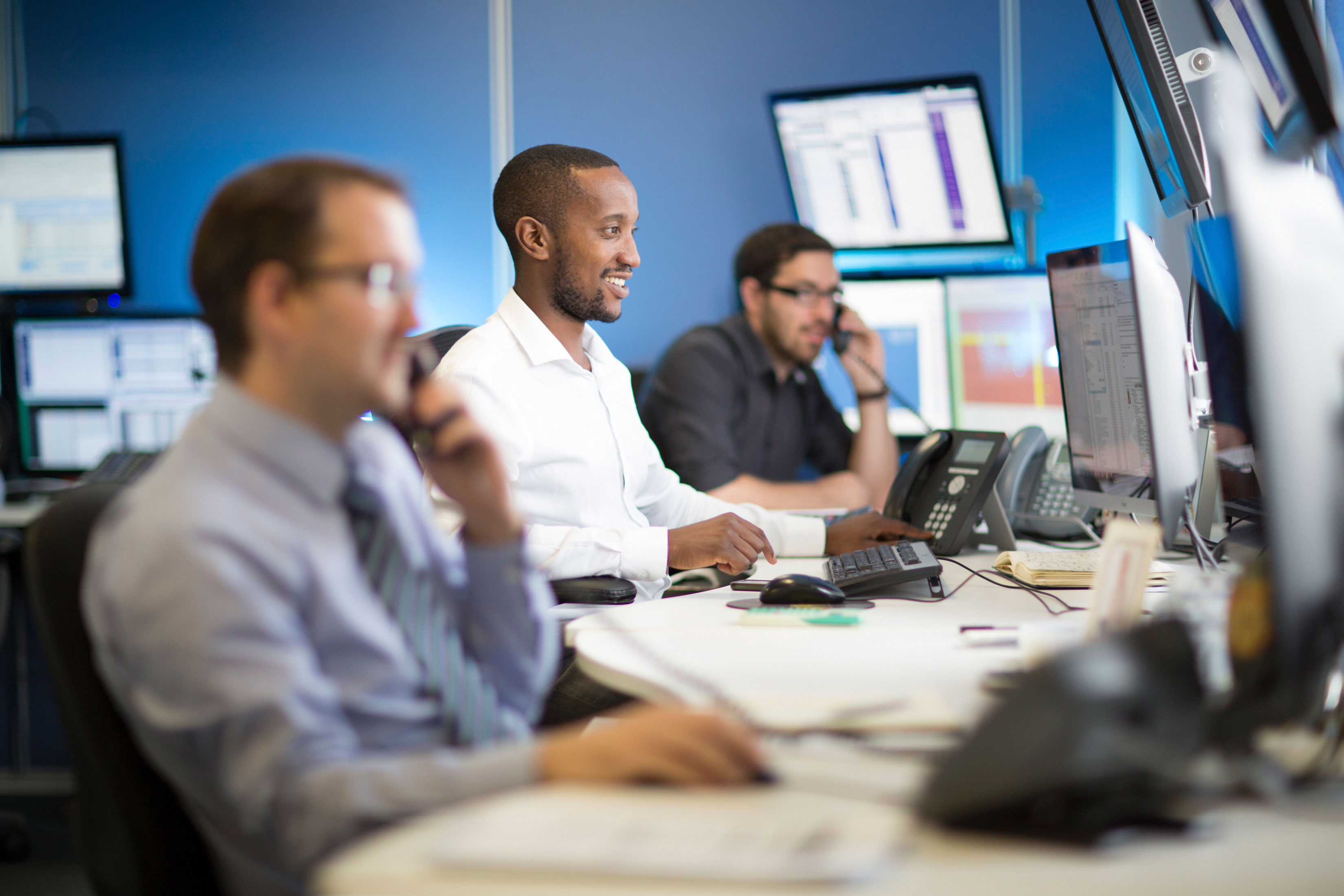
Drax Group may have been built with Drax Power Station at its core, but today it’s a set of integrated companies, helping to change the way energy is generated, supplied and used, to build a better future.
At the heart of each part of the business – from creating the fuel to power the station’s boilers to managing the supply of electricity, gas and renewable heating fuel to customers – is people.
Here we meet some of those people working behind the scenes.
Robert Gatlin, Operations Supervisor, Amite BioEnergy, Drax Biomass
“I was a student in the Process Operations Technology programme at Southwest Mississippi Community College and Drax came to the school to recruit new grads. They were introducing a new technology I’d never heard of and it sparked my interest.
“The idea of using biomass to produce electricity on such a large scale was fascinating, so I joined Drax Biomass in 2014. I was unaware biomass was being used to produce electricity – it’s very exciting to be part of something this big and cutting edge.
“One of the most interesting things I’ve discovered working here is the way moisture affects nearly everything in the pelletising process. We really have to work diligently to ensure our moisture levels are where they need to be in every stage of producing a pellet.”
Rachel Grima, Sustainability Analyst, Drax Group
“I’ve always wanted to work in renewable energy and I studied life cycle analysis during my degree. I started looking for jobs in renewable energy, and as the biggest generator of renewable energy in the UK, Drax was an obvious choice!
“Today my job involves assessing and interpreting sustainability data for all the biomass we use. Our team uses this data to assess if a supplier meets our sustainability policy and regulation.
“I’d never looked very much at transport emissions, so I find it really interesting. You can move 30,000 tonnes of wood pellets in one ship, but it would take over 1,000 trucks to move that many, creating far more greenhouse gas emissions. Since joining the team, I’ve been really surprised to see how driving small efficiencies in a supply chain can create real savings in greenhouse gas emissions.”
Stephen Wilkinson, Turbine Maintenance Technician, Drax Power Station
“I’ve always enjoyed building and fixing things. Given that my father and both grandfathers were in engineering – one of them even working at Drax during its construction – I had a strong drive to get into engineering. Living locally, it seemed the biggest and best place to work.
“I’m a Turbine Maintenance Technician, so I act as the link between the turbine support group and the main station planning and maintenance teams. I start the day early by looking through the list of overnight defects, focusing on the turbine area. After this I’m out of the office having a look at the issues to determine whether the station maintenance team or the turbine support group will carry out the repair work. From this point on every day is different.
“The recent changes Drax has made to adapt to a rapidly changing energy market has affected most people at the station. For me, seeing the major turbine upgrades take place has been extremely interesting. I started as an apprentice and then as a fitter, working on the turbine outages, seeing these upgrades first-hand. This has moved on to the point where I have been lucky enough to visit a number of the turbine manufacturing facilities in the UK and Germany.”
Gemma Baker, SME Customer Service Delivery Manager, Haven Power
“I joined Haven Power in July 2007 as a Customer Service Advisor. I’d never worked in the energy industry before and thought it sounded interesting – Haven caught my eye as it was a new company which excited me. Being part of and contributing to a growing company was right up my street!
“Now I’m responsible for delivering a consistent and valued account management service to our electricity customers across all the small- to medium enterprise (SME) segments. This includes everything from billing and cash collection, to renewals and query and complaint resolution. I’ve been at Haven for nine and a half years now!”
Sam French, Customer Service Administrator Apprentice, Opus Energy
“Before joining [Opus Energy] I didn’t know anything about the energy industry – now I know about different supplier competitors, how an electricity supply contract is agreed and registered, and how we actually apply for a supply. I’ve learnt so much about different aspects of the energy industry, too.
“I haven’t had that much involvement with the Drax Group yet, but I’ve enjoyed looking into the business. I’ve found it really interesting to learn how they’ve managed to transition from a non-renewable company to one that is now producing more renewable than fossil fuel power – which is amazing.”
Amy Carton, Sales and Marketing Executive, Billington Bioenergy
“I’m responsible for all aspects of internal and external marketing and communications at Billington Bioenergy, a company which supplies wood pellets to commercial and domestic customers who use them to heat their homes or businesses.
“I try to be environmentally conscious and keep my carbon footprint as low as possible – renewable and sustainable heating comes into this. It’s wonderful to spend my days promoting the merits of renewable heating. It’s a relatively small industry in the UK in comparison to our European counterparts, but this makes what we do here in Billington Bioenergy quite unique.
“There was quite a bit of information to digest when I first started – for example, ENplus regulations, different types of pellets, how wood pellet boilers work… it was a big learning curve!”