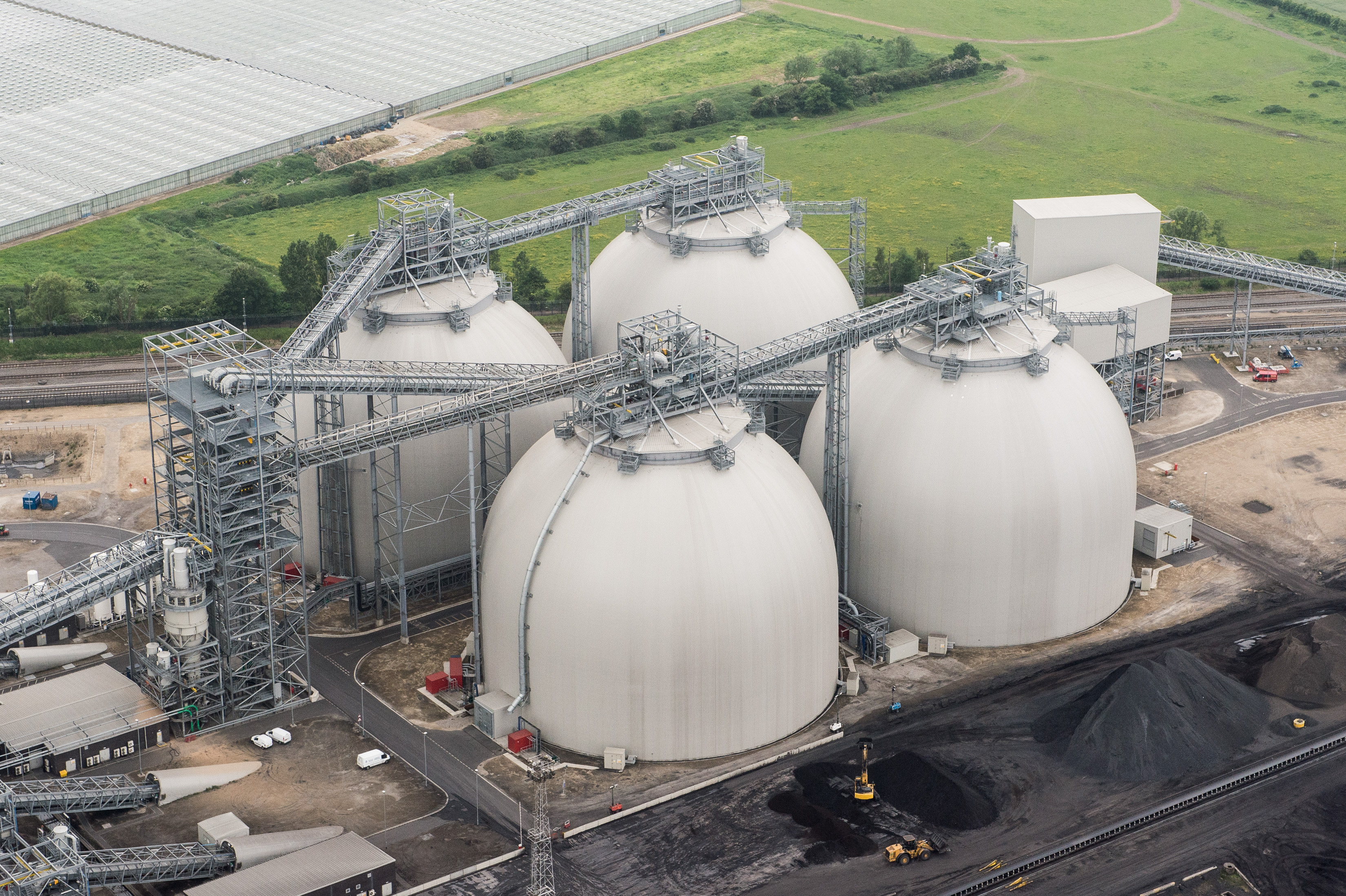
By 2025, the UK will face a 40-55 per cent gap between electricity supply and demand, according to a report from the Institute of Mechanical Engineers. The government has disputed IMechE’s projection but its own forecasting suggests that UK electricity demand will be 19% higher in 2035 vs. 2015.
The alleged 2025 gap will be caused by the closure of coal-fired power stations to meet targets for carbon reduction. According to the IMechE, current plans to plug the gap by building new gas-fired capacity are unrealistic. (It would require a staggering 30 new power stations to be planned and built from scratch within the next 10 years.)
At Drax, we have already developed a solution. We can do it quickly, cheaply and safely. In fact, it would drastically reduce the time and money involved in building all of those 30 new gas power stations from scratch.
We’ve already adapted three of our coal-fired generating units to use high-density pellets made from compressed low-grade wood. And we’re using world-beating technology developed by our own engineers here in the UK to do it.
In all, around four or five per cent of the UK’s entire electricity needs every single day of the year are already being met thanks to our unique biomass technology at Drax. It’s an approach that could be adopted elsewhere in the country, providing a huge contribution to plugging the electricity gap.
Our high-density compressed wood pellets are the only non-fossil fuel that can bring about these changes in the time we have left.
Given the right support, within two or three years, we could convert the remaining three units at Drax power station to run on biomass wood pellets.
With all six units converted, plus Lynemouth power station – which already has that future secured – and one or two other, smaller biomass power stations, around 10 per cent of the UK’s electricity could be generated using this technology well before 2025 – long before new gas-fired capacity could come on stream.
The costs involved would be dramatically lower too. We invested around £650 million to convert three generating units, develop a supply chain and build new storage at Drax. It is estimated that the equivalent in new combined cycle gas turbine power stations would cost more as it would be new rather than repurposed infrastructure.
Energy hierarchy
The IMechE has developed an energy hierarchy, listing five sustainability-related priorities against which to judge any future energy strategy. The two that focus on energy generation are a perfect fit in terms of coal-to-biomass conversions at Drax and Lynemouth.
“Priority 3 – utilisation of renewable, sustainable resources”
High density compressed wood pellets are made from low-grade wood sourced according to the highest levels of forestry conservation.
“Priority 5 – utilisation of conventional resources as we do now”
Using world-leading engineering skills and avoiding the need to build brand new power stations, our coal units can be converted without the need for new National Grid connections.
Many of our European neighbours such as Sweden and Germany already use a far higher proportion of biomass to meet their energy needs. Catching up with the European average is the simplest, quickest and most affordable way to avoid a shortfall between supply and demand predicted by 2015.