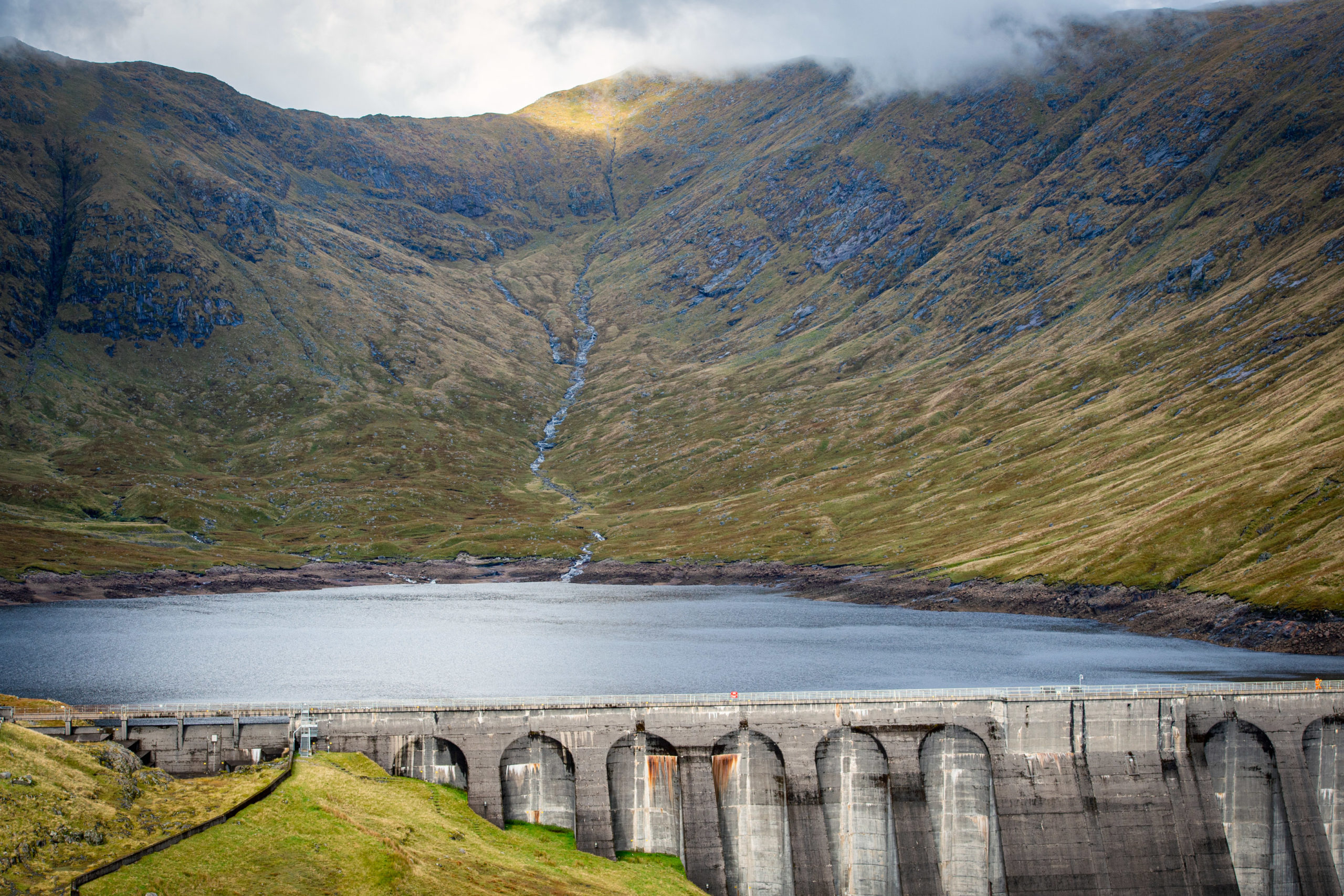
Key points:
- Energy storage plays a crucial role in the UK electricity system by not only providing reserve power for when demand is high but also absorbing excess power when demand is low.
- The UK’s electricity system’s growing dependency on intermittent renewables means the amount of energy storage needed will increase to as much as 30 GW by 2050.
- There are three different durations of energy storage needed to help balance the grid: short-term, day-to-day and long term.
- It will take a range of technologies including batteries, pumped storage hydro and new approaches to meet the storage demands of a net zero grid.
When you turn on a lightbulb – in 10, 20, or 30 years – the same thing will happen. Electricity will light up the room. But where that electricity comes from will be different. As the country moves toward net zero emissions, low carbon and renewable power sources will become the norm. However, it’s not as simple as swapping in renewables for the fossil fuels the grid was built around.
Weather dependant sources, like wind and solar, are intermittent – meaning other sources are needed at times when there’s little wind or no sunshine to meet the country’s electricity demand. Equally as challenging to manage, however, is what to do when there’s an excess of power being generated at times of low demand.
Energy storage offers a low carbon means of delivering power at times of low supply, as well as absorbing any excess of generated power when demand is low, helping to balance and stabilise the grid. As the electricity system transforms through a range of low-carbon and renewable technologies, the amount of energy storage on the UK grid will need to expand from 3 GW of today to over 30 GW in the coming decades.
The storage solution
Even as the UK’s electricity system transforms, from fossil fuels to renewables, the way the grid operates remains primarily the same. Central to that is the principle that the supply of electricity being generated must always match the demand on a second-by-second basis.
Too little or too much power on the system can cause power outages and damage equipment. National Grid needs to be able to call on reserve power sources to meet demand when supply is low or pay to curtail renewable sources’ output when demand drops. During the summer of 2020, for example, lower demand due to Covid-19 coupled with high renewable output resulted in balancing costs 40% above expectations.
“There is a lot of offshore wind coming online in Scotland, as much as 11 GW by 2030 and a further 25 GW planned,” explains Steve Marshall, a Development Manager at Drax.
Offshore wind farm along the coast of Scotland
“It’s great because it increases the amount of renewable power on the system, but the transmission lines between Scotland and England can become saturated as much as 30-40% of the time because there is too much power.”
Electricity storage can provide a source of reserve power, as well as absorb excess electricity. These capabilities are crucial for balancing the grid and ensuring that frequency remains within a stable operating range of 50 Hertz, as well as providing other ancillary services.
Whether it’s absorbing power or delivering electricity needed to keep the grid stable, in energy storage, timing is everything.
There are three main time periods electricity storage needs to operate over:
-
Fast-acting, short term electricity
Because electricity supply must always match demand, sudden changes mean the grid needs to respond immediately to ensure frequency and voltage remain stable, and electricity safe to use.
Batteries are considered the fastest technology for responding to a sudden spike in demand or an abrupt loss of supply.
Battery technology has evolved rapidly in recent decades as innovations like lithium-ion batteries, such as those used in electric cars, and emerging solid-state batteries become more affordable and more commonplace. This makes it more feasible to deploy large-scale installations that can absorb and store excess power from the grid.
“Batteries are good for near-instantaneous responses. It can be a matter of milliseconds for a battery to deploy power,” says Marshall. “If there’s a sudden problem with frequency or voltage, batteries can respond – it’s something that’s quite unique to them.”
The speed at which batteries can deploy and absorb electricity makes them useful grid assets. However, even very large battery setups can only discharge power for around two hours. If, for example, the wind dropped off for a long period the grid needs a longer-duration supply of stored power.
-
Powering day-to-day changes in supply, demand, and the grid
When it comes to managing the daily variations of supply and demand the grid needs to be able to call on reserves of power for when there are unexpected changes in the weather or electricity demand from users. Pumped storage hydro power offers a low carbon way to provide huge amounts of electricity, quickly and for periods that can last as long as eight or even 24 hours.
The technology works by moving water between two reservoirs of water at different elevations. When there is demand for electricity water is released from the upper reservoir, which rushes down a series of pipes, spinning water turbines, generating electricity. However, when there is an excess of power on the electricity system the same turbines can reverse and absorb electricity to pump water from the lower to the upper reservoir, storing it there as a massive ‘water battery’.
Pumped storage hydro is a long-established technology, having been developed since the 1890s in Italy and Switzerland. In the UK today there are four pumped storage hydro power stations in Scotland and Wales, with a total capacity of 2.8 GW.
Among those is the Drax-owned Cruachan Power Station in the Scottish Highlands. The plant is made up of four generating/pumping turbines located inside Ben Cruachan between Loch Awe and an upper reservoir holding 10 million cubic metres of water.
Turbine Hall at Cruachan Power Station
Pumped hydro storage facilities can rapidly begin generating large volumes of power in as little as 30 seconds or less. The ability to switch their turbines between different modes – pump, generate, and spin mode to provide inertia to the gird without producing power – make pumped storage hydro plants versatile assets for the gird.
“How Cruachan operates depends on weather,” says Marshall. “We make as many 1000 mode changes a month, that’s how frequently Cruachan is called on by National Grid.”
As the electricity system transforms there will be a greater need for flexible energy storage like pumped storage hydro, this is why Drax is kickstarting plans to expand Cruachan Power Station, however, the specific conditions needed for such facilities can make new projects difficult and expensive.
Cruachan 2, to the east of the original power station, will add up to 600 MW in generating capacity, more than doubling the site’s total capacity to more than 1GW. By increasing the number of turbines operating at the facility it increases the range of services that the grid can call upon from the site.
-
Long-term electricity solutions
However, storage technologies as they exist today cannot alone offer all the solutions the UK will need to achieve its net zero targets. While technologies like pumped storage can generate for the better part of a day, longer periods of unfavourable conditions for renewables will need new approaches.
In March 2021, for example, the UK experienced its longest cold and calm spell in more than a decade, with wind farms operating at just 11% of their capacity for 11 days straight, according to Electric Insights.
The shortfall in the country’s primary source of renewable power was made up for by gas power stations. But in a net zero future, such responses will only be feasible if they’re part of carbon capture and storage systems or replaced by other carbon neutral or energy storage solutions.
Generating enough power to supply an electrified future, as well as being able to take pressure off the grid and provide balancing services will require a range of technologies working in tandem over extended periods.
Interconnectors with neighbouring countries, for example, can work alongside storage solutions to shed excess power to where there is greater demand. Similarly, rather than curtailing wind or solar power, extra electricity could be used for electrolysis to produce hydrogen. Other functions may include demand side response where heavy power users are incentivised to reduce their electricity usage during peak periods helping to reduce demand.
To achieve stable, reliable, net zero electricity systems the UK needs to act now to not only replace fossil fuels with renewables but put the essential energy storage and balancing solutions in place, that means electricity is there when you turn on a lightbulb.