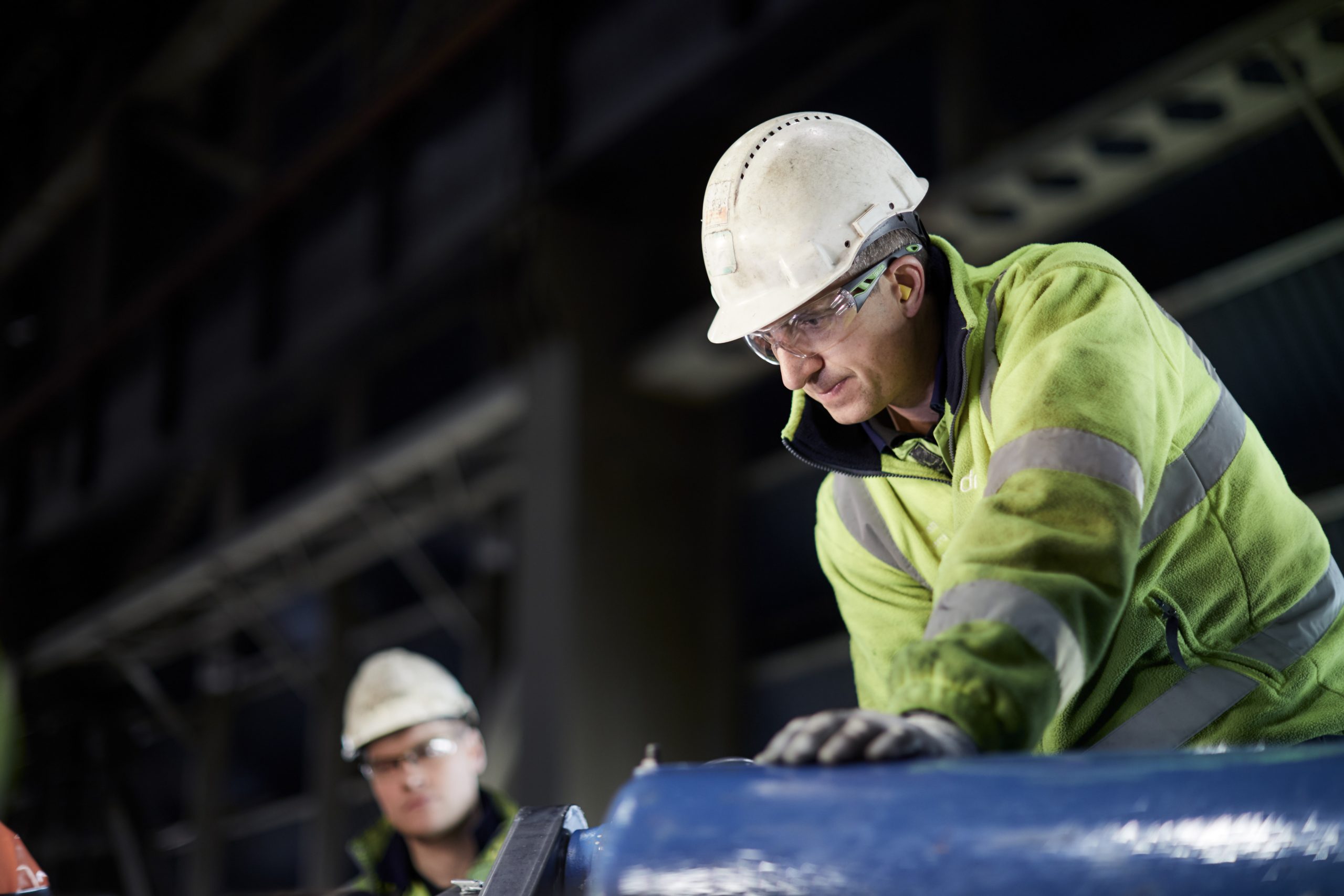
We are living through unprecedented times. Coronavirus is having far reaching effects on all industries not just here in the UK, but around the world. At Drax, we take our responsibilities as a member of critical national infrastructure and as an essential service provider very seriously. We are committed to maintaining a continuous, stable and reliable electricity supply for millions of homes and businesses in the UK.
The wellbeing of our people
Firstly, I’d like to thank our employees, contractors, supply chain workers and their families as well as the communities in the UK and US in which we operate, for their fantastic support and continued hard work during these difficult and uncertain times. Our employees’ health and wellbeing are vital, and we’re working hard to ensure we are supporting them with both their physical and mental health, whether working at home or at one of our sites.
Across all our sites we are have implemented strategies to reduce the chances of people spreading the virus and have operational plans in place to ensure continued delivery of power into the grid.
Power station resilience
At Drax Power Station, the UK’s largest power station, largest decarbonisation project in Europe and biggest source of renewable power into the national grid, we have arranged for the separation of key operational teams and employees so that they are physically distanced from each other. We have moved as many employees as possible to work from home, so that there are fewer people in our workplaces reducing the risk of the spread of infection, should it arise. We have strict controls on visitors to the site and on our contractors and suppliers. Our resilience teams are working well and we have contingency plans in place to manage risks associated with colleague absences.
We have closed the visitor centres at Cruachan pumped storage hydro power station and Tongland hydro power station in Scotland, as well as at Drax Power Station in North Yorkshire. We have also stopped all but critically important travel between our sites.
Our supply chain
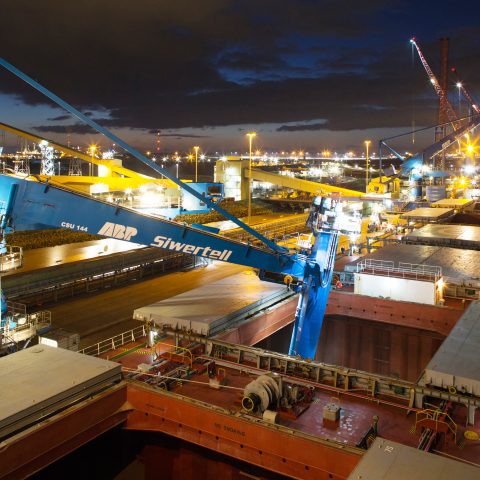
Sustainable biomass wood pellets destined for Drax Power Station unloaded from the Zheng Zhi bulk carrier at ABP Immingham [Click to view/download]
Just last week Associated British Ports (ABP) and Drax received and unloaded the largest ever shipment of sustainable biomass to arrive at the Port of Immingham in the UK’s Humber region. The vessel transported 63,907 tonnes of Drax’s wood pellets from the US Port of Greater Baton Rouge in Louisiana. The consignment supplies Drax Power Station with enough renewable fuel to generate electricity for 1.3 million homes.
Our three wood pellet manufacturing plants are running well, with US authorities classifying our employees as key workers. The same is the case for our rail freight partners on both sides of the Atlantic. In the UK, GB Railfreight recognises the strategic importance of biomass deliveries to Drax Power Station.
Our customers
Businesses – both large and small – are feeling the economic effects of this virus. Our employees involved with the supply of electricity, gas and energy services to organisations are working hard to support them. More information can be found via these links:
We are working closely with BEIS, HM Treasury and our trade associations to explore how government and industry can further support business through this challenging time. Organisations facing financial difficultly can access the unprecedented level of support already announced by the Chancellor, Rishi Sunak via:
- Department for Business, Energy and Industrial Strategy (BEIS)
- HM Government Coronavirus Business Support
Leadership
Our Executive Committee is meeting regularly via video conference to discuss our contingency planning as the situation changes. We are working closely with the UK, US state and Canadian governments, National Grid and Ofgem to ensure that we remain up to date with the latest advice and that we are prepared for any further escalation.
This is an unprecedented time for the UK and the world. Rest assured that Drax’s critical national infrastructure and essential service operations, as well as its employees, are working hard 24/7 to make sure individuals, families, businesses and organisations are supplied with the vital electricity needed to keep the country running.